Do you have a welded assembly project? Request a personalized quote
Welded assemblies with high-quality finishes
Welding methods: precision and reliability for every need
TIG (Tungsten Inert Gas) welding
An electric arc welding process that uses a non-consumable tungsten electrode. This method allows for high-quality welding with precise control of the material melt, and is ideal for welding on thin materials and in environments that require a clean, impurity-free finish.
DIFFERENTIATING FEATURES
- High quality and precision in welding
- Ideal for thin and delicate materials
- Aesthetically impeccable, slag-free finish
EXAMPLES OF MATERIALS
- AISI 316
- AISI 304
- Titanium
- Precise welds with excellent penetration control and without the formation of slag, ensuring a perfect aesthetic finish
MIG (Metal Inert Gas) welding
An electric arc welding process that uses a continuous wire as filler material and an inert gas to protect the arc from contamination. It is widely used for fast, efficient welding on thicker thicknesses than TIG, offering good penetration and high productivity.
DIFFERENTIATING FEATURES
- Faster welding speed
- Ideal for thick materials and high-production jobs
- Ease in process automation
EXAMPLES OF MATERIALS
- AISI 316
- AISI 304
- Carbon
- Ability to weld quickly on higher thicknesses, reducing processing time and ensuring strength and durability of the welds.
Arc welding with coated electrode
Shielded Metal Arc Welding (SMAW) is one of the most common welding methods, using a coated electrode to generate the electric arc. This method is particularly advantageous for working outdoors or in situations where a shielding gas cannot be used.
DIFFERENTIATING FEATURES
- Ideal for outdoor work or in windy environments
- Easy to use even for welding on thicker thicknesses
- Excellent ability to weld upright or overhead.
EXAMPLES OF MATERIALS
- AISI 316
- AISI 304
- Carbon Steel
- It can be used in harsh environments and allows for strong and durable welds on a wide range of materials.
Online quotation
Request a quote in just a few steps through our RFQ system dedicated to welded assemblies.
Upload your files, select the materials and the desired finish, then send the request to receive a personalized quote.
It is important that all welding specifications are clearly stated in the table. In the absence of indications, a standard spot weld will be applied. You can track the progress of your project directly from your account, with a digital, transparent, and efficiency-oriented process.
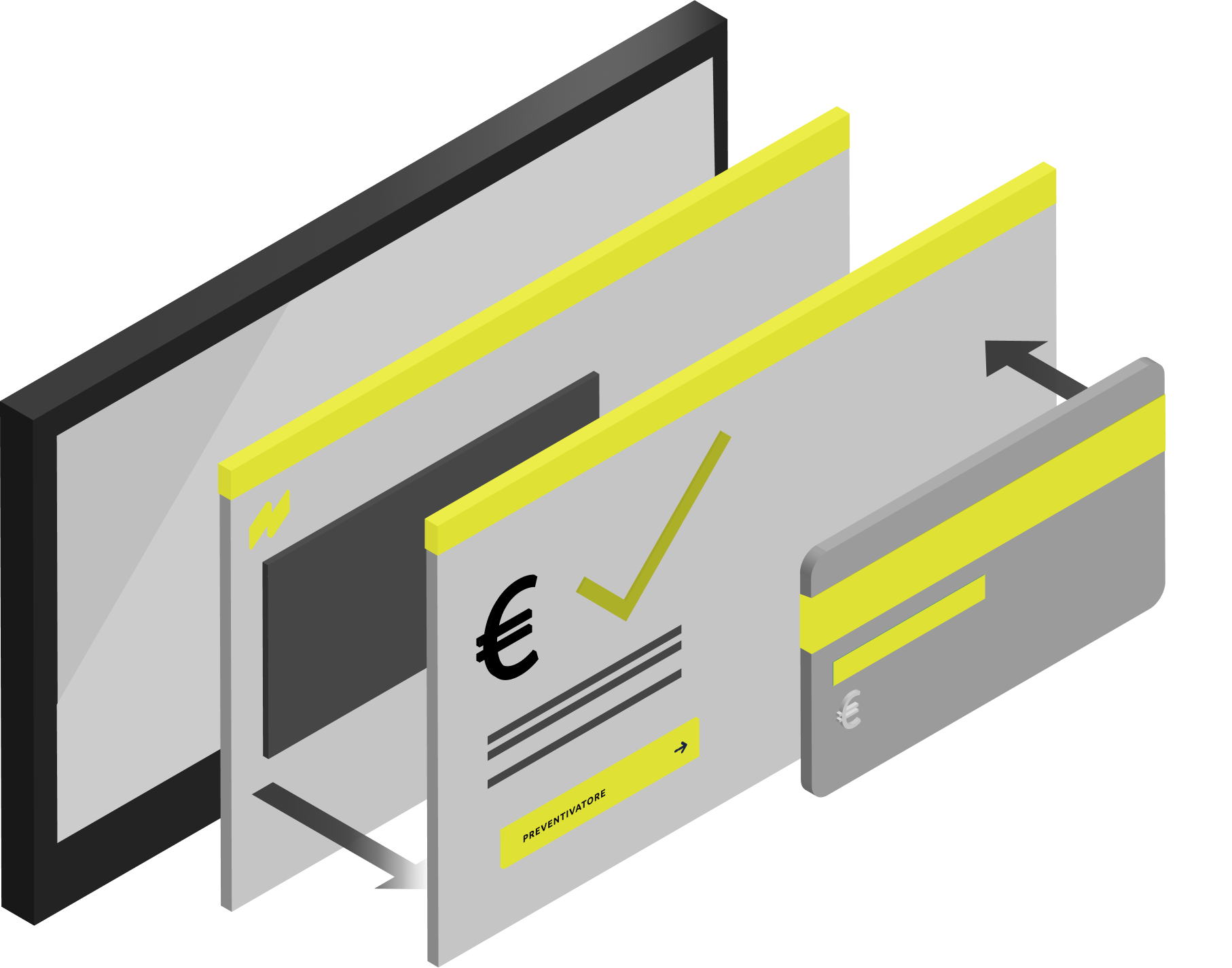
OPTIMIZED PROCESSES
We manage the production of welded assemblies through structured and controlled workflows, integrating cutting, machining, welding and finishing. An efficient approach that reduces time, costs and margins of error, ensuring constant quality even on complex productions.
RAPID PROTOTYPING
We create prototypes of welded assemblies in a short time, with high precision and construction quality. A service designed to facilitate the verification, adaptation and optimization phases of the project before the final production.
HIGH PERFORMANCE
We manufacture custom-made welded assemblies, designed to ensure structural strength, dimensional accuracy and reliability even in the most demanding applications. A complete service, from the machining of the individual components to the final integration.
PRODUCTION TECHNOLOGIES
Welded assemblies are one of our most robust and versatile solutions. Thanks to advanced welding technologies and accurate control of each step, we create structures that are reliable, precise and ready for integration into complex systems.
Welded assemblies: precision, reliability and customized solutions for companies
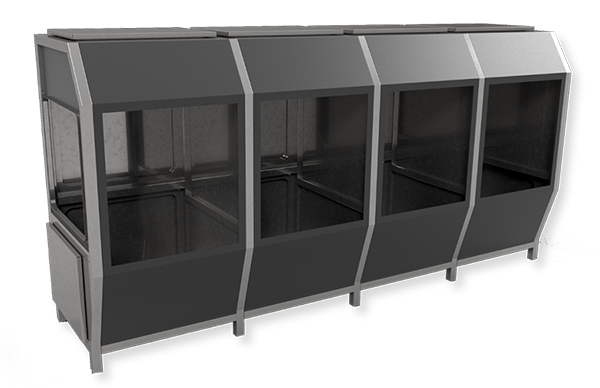
Precision
and Reliability
Thanks to a consolidated experience in the sector and the use of advanced production technologies, we guarantee high precision in the execution of welded assemblies and full reliability in the dimensional and functional requirements required by the project.
Full customization
We operate on the basis of technical drawings and specifications provided by the customer, offering maximum flexibility in the choice of materials, treatments and finishes, to adapt precisely to the needs of each project.
Integration into the Production Cycle
The welding process is perfectly integrated with the other mechanical and finishing processes, ensuring operational fluidity and optimized times.
Control
and Quality
We pay great attention to the quality of each welded assembly, ensuring that each process is carried out with precision and in compliance with the specifications of the project.
Not sure which method to choose?
Discover the ideal solution for your project. Our team of experts is on hand to help you select the welding technology and process that best suits your needs.
Choosing the right weld makes all the difference.
Each project requires the most suitable type of welding to ensure solidity, precision and functionality. The different welding configurations differ not only in the method used, but also in the final application: the selection depends on the characteristics of the workpiece, the technical requirements and the objectives of the project.
The right weld for your project. The choice of the type of welding directly affects the mechanical strength, aesthetic quality and functionality of the assembly. Among the most widely used solutions are butt, spot, continuous and overlap welding, each with specific characteristics based on geometry, materials and final application. Below is an overview of the four main weldment configurations used to guide you in selecting the right fit for your project.
Welding
head
Technique used to join two metal elements along the opposing edges. It provides a solid connection, ideal for applications that require robustness and precision.
Welding
points
It consists of the localized joining of two parts through distributed welding points. It is a fast and efficient solution, particularly suitable for high-speed production and automated cycles
Welding
continuously
It involves welding along the entire length of the joint, ensuring a uniform seal and a linear finish. Suitable for extended or thin-walled components, where structural consistency is required.
Overlay welding
Two elements are overlapped and joined along the top edge. This technique ensures continuous and strong adhesion, and is frequently used for multi-layer or sheet metal assemblies.
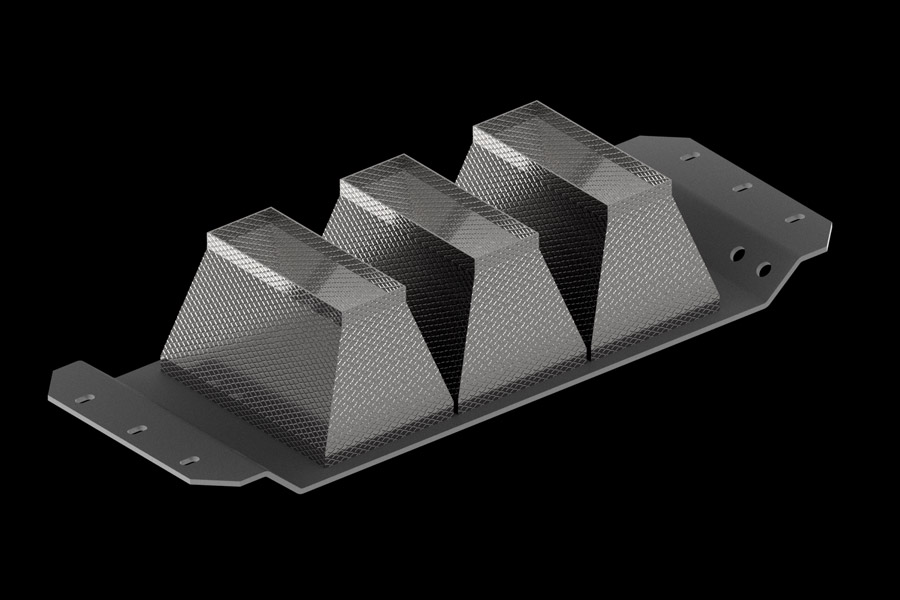
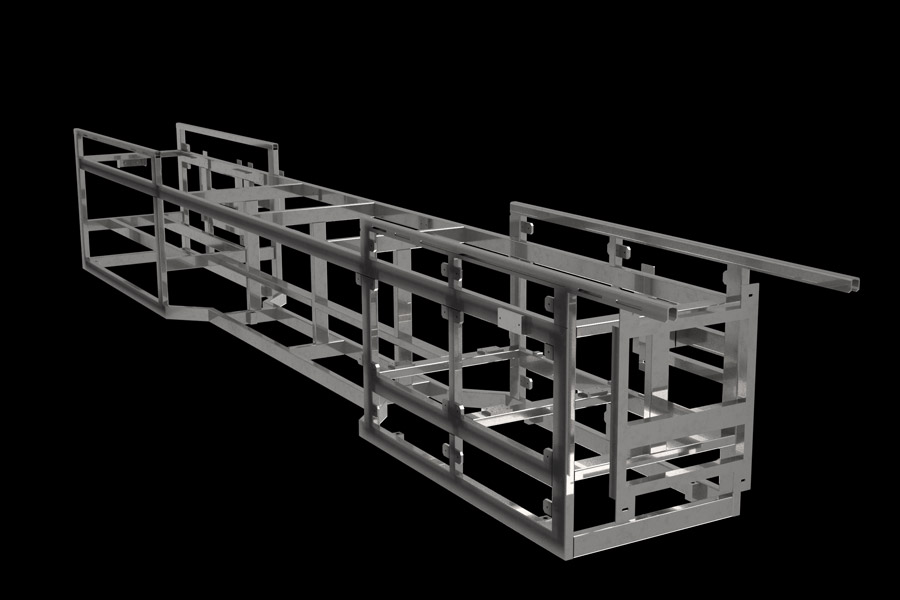
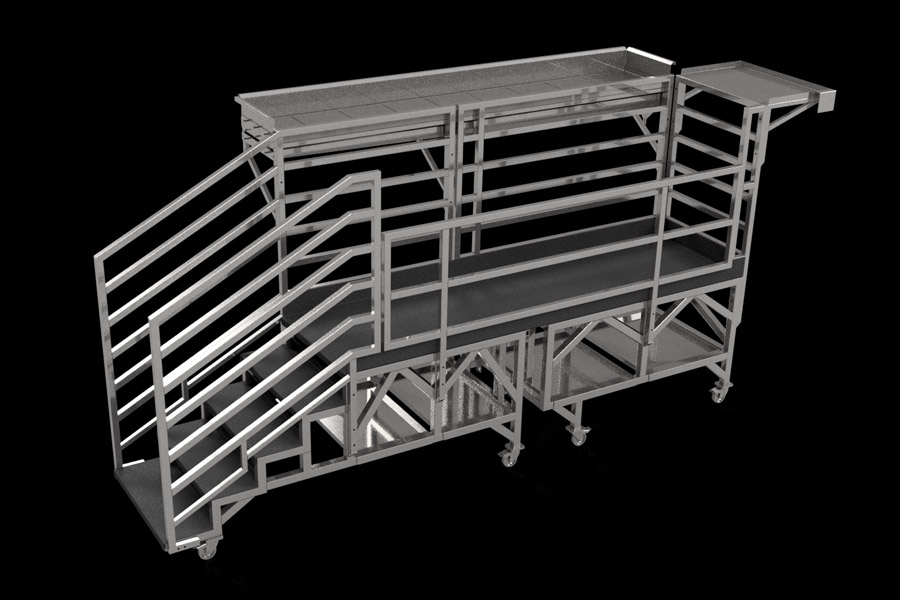
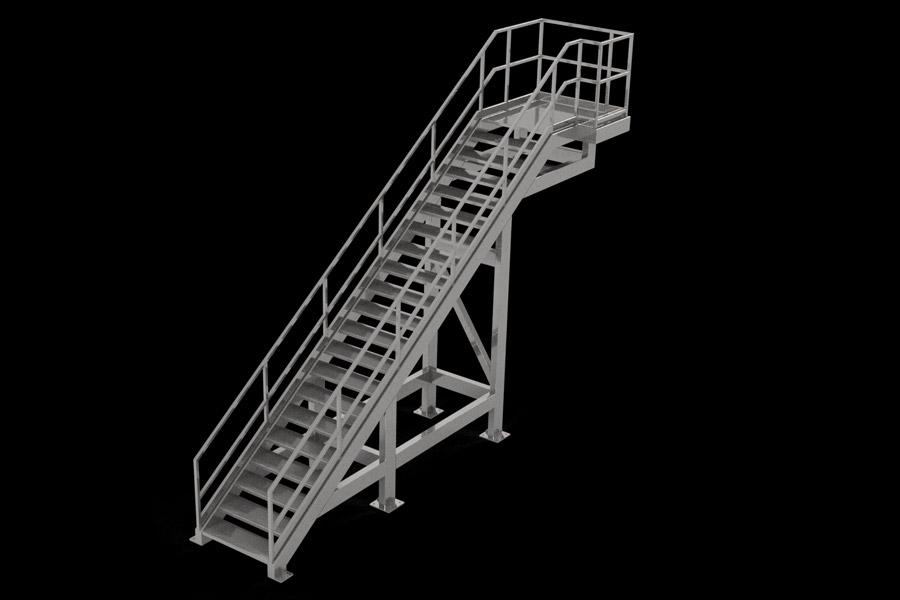
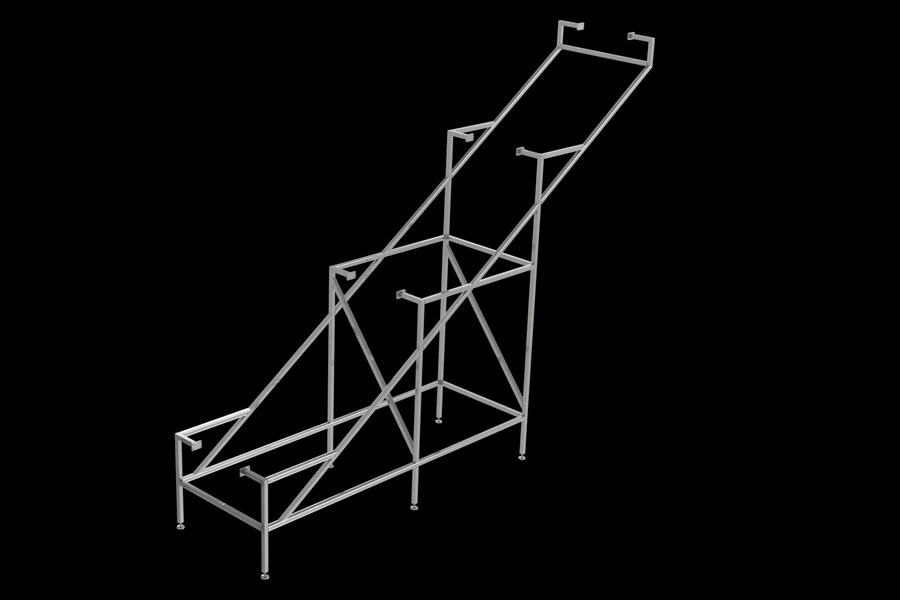
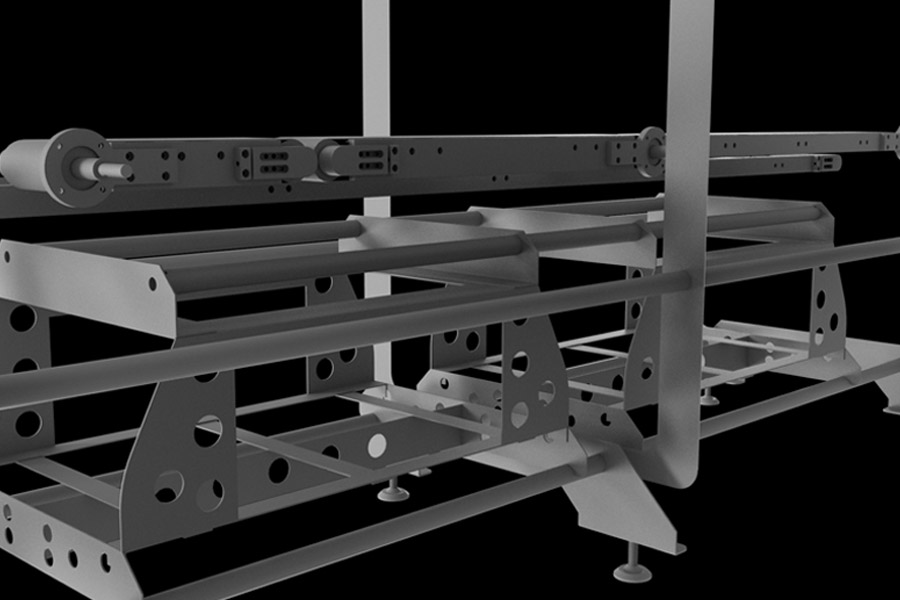

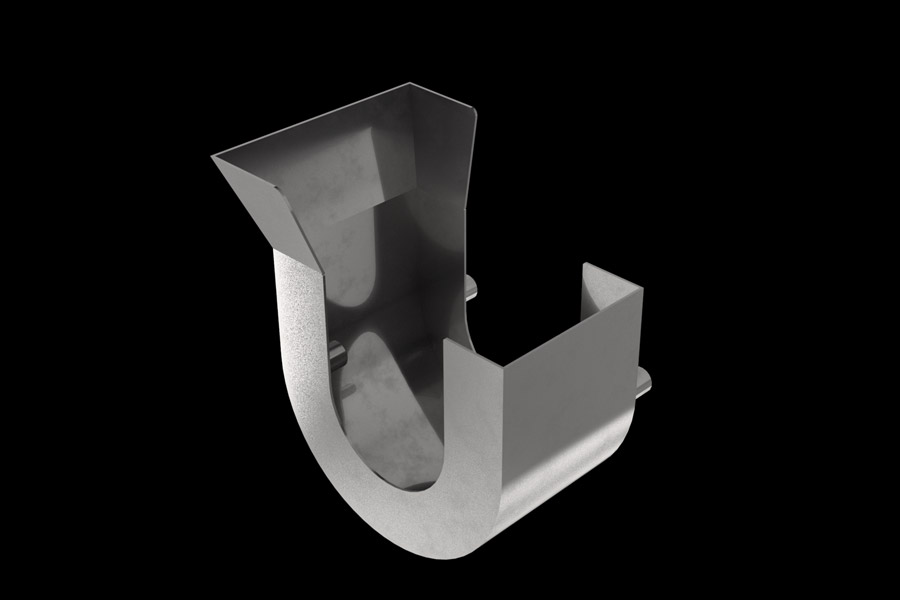
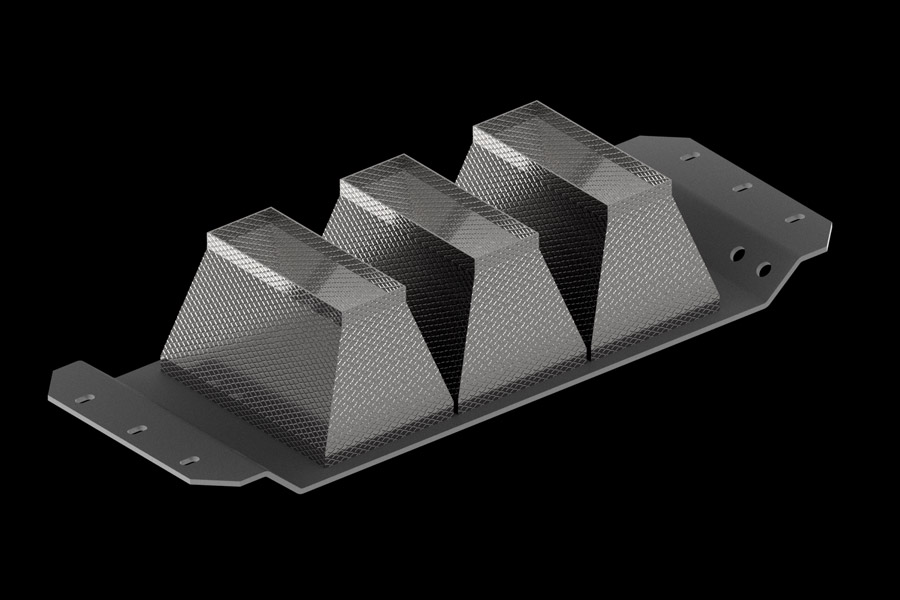
Benefits of Welded Assemblies: Effective Solutions for Complex Structures
High structural strength
Welded assemblies are designed to ensure mechanical stability, rigidity and reliability over time, even under intense load or stress conditions.
The correct choice of geometry, materials and welding technique results in robust structures that are suitable for high-performance industrial applications.
Flexibility in Shapes and Design
The creation of welded assemblies allows elements with different geometries to be combined, facilitating the production of structures that cannot be obtained from a single block.
This solution is particularly suitable for projects that require modularity, dimensional customization or functional adaptations, while ensuring structural integrity and construction precision.
Compatibility with Different Types of Materials
We precisely manage the welding of stainless steels, in particular AISI 304 and AISI 316, known for their mechanical and corrosion resistance.
Our processes ensure reliable and consistent joints, even on complex geometries or components with high requirements.
The choice of material is made by the customer during the design phase, while we ensure the correct execution based on the technical characteristics and specifications provided.
Reduced Production Costs
Through optimized processes, integration between processes and centralized management of the entire production cycle, we are able to contribute in a concrete way to the rationalization of costs, maintaining high quality standards and certain times.
Compatible Materials for Welded Assemblies
Our machining technology can transform selected stainless steels, including AISI 304 and AISI 316, which are known for their mechanical and corrosion resistance.
Post-processing and finishing for parts made with welded assembly machining
Pickling
Pickling is an essential process for obtaining clean metal surfaces ready for further treatment. Using specific chemical agents, it removes oxides, calamine and welding residues, improving not only the aesthetic appearance but also the resistance to corrosion.
- Effective removal of oxides and impurities
- Smooth and uniform surface
- Increased corrosion resistance
- Ideal preparation for protective coatings
- Optimization of product life and performance
Glass sandblasting
Glass blasting is a surface finish that uses glass granules to remove impurities and oxides, giving it a matte and uniform appearance. It is perfect for preparing metals for painting or other treatments, improving both aesthetics and functionality.
- Removal of impurities and surface oxides
- Homogeneous and matt surface
- Improved adhesion for paints or coatings
- Increased mechanical properties of the surface
- Ideal finish to prepare the material for subsequent treatments
Frequently asked questions
RFQ Quote: Get a detailed quote for machining, services, and finishes.
How can I receive a personalized quote?
To receive a custom quote, you must submit an RFQ (Request For Quotation). This process allows us to analyze the details of your project, understand your specific needs, and provide you with an accurate and timely proposal.
How long does it take to get a quote?
Listing times are usually quick. Once we receive the details of the project, we work to provide you with an estimate as soon as possible, allowing you to have clarity on costs without unnecessary delays.
How long does it take to produce a welded assembly?
Production times depend on the specifics of the project, such as the complexity of the design, the materials chosen and the finishes required. We work with flexible times, but always guarantee an efficient and punctual process.
Why choose welding for assembly making?
Welding technology enables complex assemblies that could not be achieved with other technologies, such as solid machining. Using welding to create a component is often the ideal solution for obtaining strong, precise and functional structures that are difficult to achieve with other machining methods.
What advantages does welding offer in the production of structural parts?
Welding allows various metal components to be permanently joined, ensuring high mechanical strength and structural stability.
This technique is particularly advantageous in the production of complex parts, as it allows you to optimize costs, reduce the number of processes and create geometries that would not be obtainable from a single block of material.
It also offers greater flexibility in design, facilitates modular interventions and allows the use of high-performance materials, such as AISI 304 and 316 stainless steels, without compromising properties.