Print without limits with HP Multi Jet Fusion technology
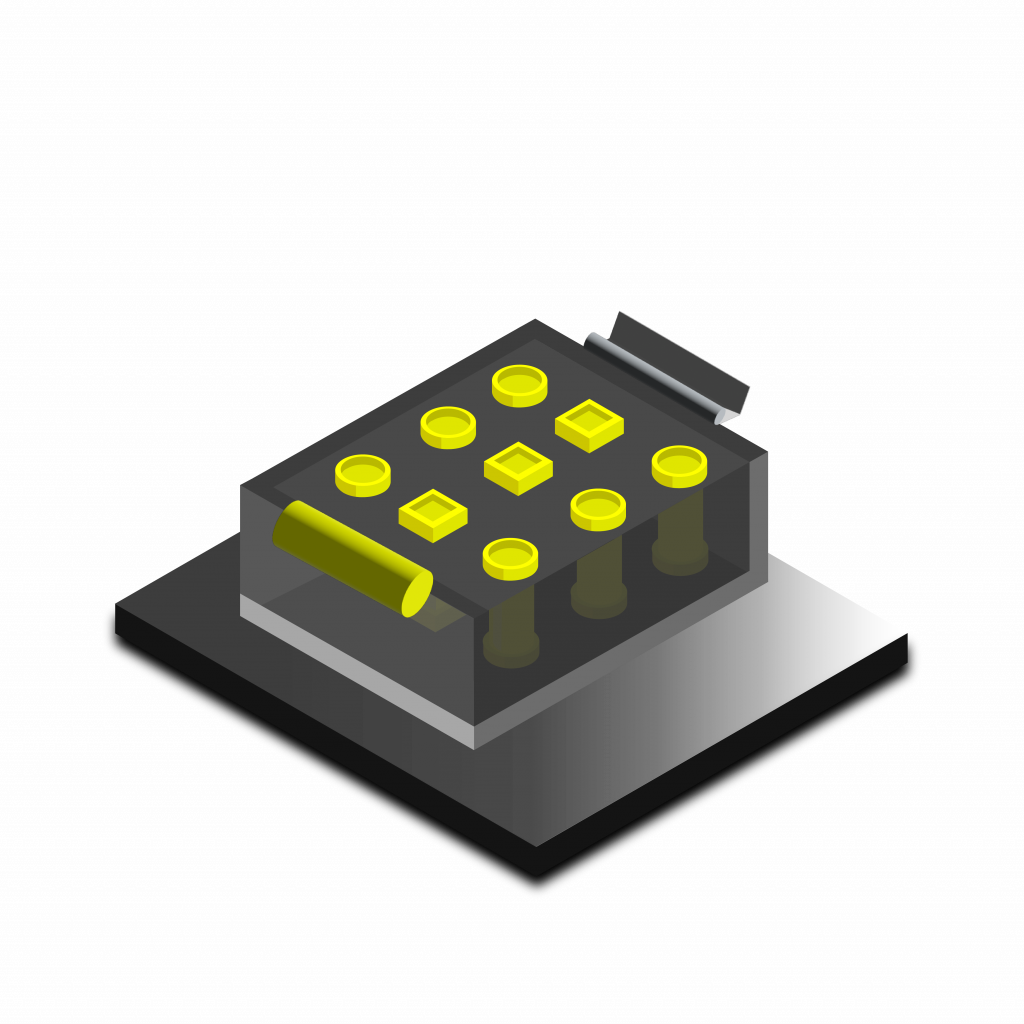
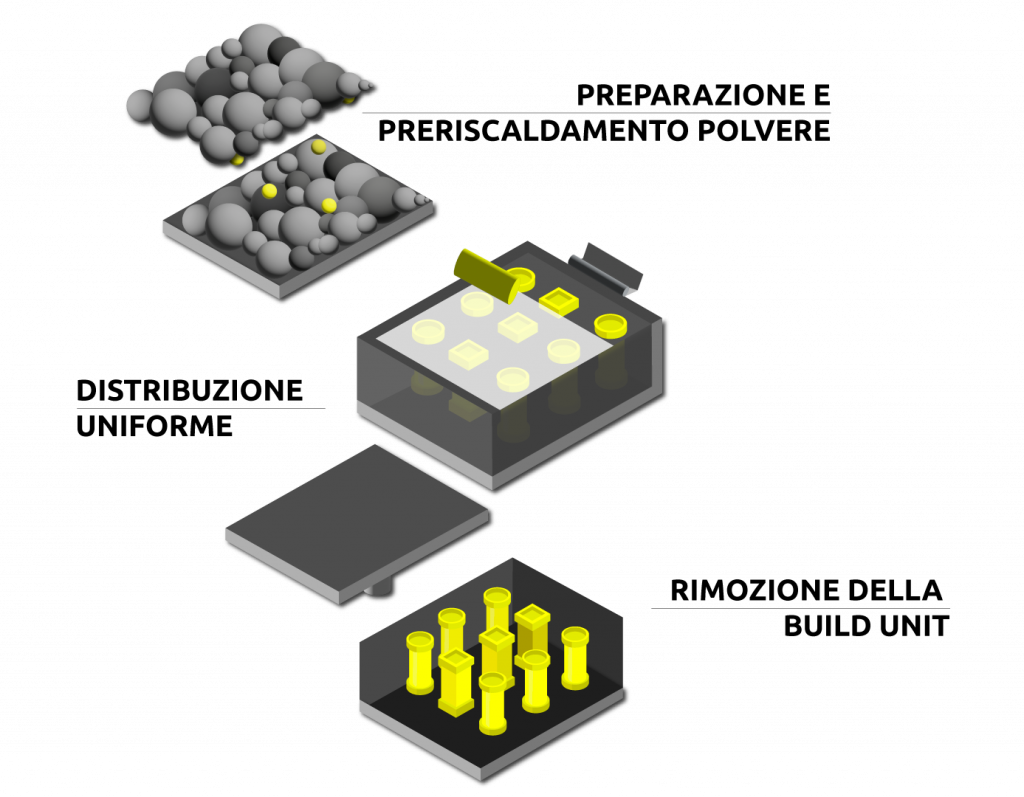
How HP MJF technology works
High-precision 3D printing for complex, functional, and repeatable parts
HP Multi Jet Fusion (MJF) is a powder bed 3D printing technology designed for the industrial production of functional parts with reliable mechanical characteristics, high geometric accuracy, and reduced cycle times compared to other additive technologies. Unlike processes such as laser sintering (SLS), MJF uses a multi-agent deposition system combined with selective laser sintering.
HP Multi Jet Fusion Printing Process
During the process, a thin layer of polymer powder material is spread evenly on the work surface. Inkjet heads selectively distribute two types of agents:
- Melting agent, which promotes heat absorption in the desired areas;
- Detailing agent, which controls the edges and improves the definition of surfaces.
Next, an infrared heat source selectively activates the voxels (the three-dimensional “pixel volumes”) in the areas treated with the melting agent, causing the polymer particles to be precisely welded. The result is a solid, isotropic part characterized by excellent mechanical strength, high dimensional accuracy and uniform surface finish.
Benefits and Applications of MJF Technology
Thanks to its high repeatability and the possibility of producing medium to large series in a short time, MJF technology is ideal for:
- Functional and testable prototypes;
- Final components;
- Complex parts with fine details and thin walls;
- On-demand and just-in-time production.
MJF also stands out for optimizing powder use, with a significant percentage of recycled material in the production cycle, making it a more sustainable choice than other powder bed processes.
01 – Material Preparation
A thin, uniform layer of polymer powder is deposited on the work area, forming the initial basis for the layer-by-layer construction of the component.
02 – Preheating the powder
The newly distributed powder is preheated to a controlled temperature (about 165°C), optimizing the cohesion between particles and promoting uniform melting in the subsequent phases.
03 – Uniform material distribution
A roller slides along the Y-axis distributing a constant layer of powder, with an average thickness of about 80 μm, ensuring regularity and continuity in the additive process.
04 – Agent Application
The printheads deposit two types of agents: the melting agent, which defines the areas intended for sintering, and the detailing agent, which improves contours and surface quality.
05 – Selective Fusion
The areas treated with the melting agent are thermally activated, causing the polymer particles to save. The detailing agent allows for better geometric control of surfaces.
06 – Layered Part Formation
Through the combination of agents and heat, the powder progressively melts layer by layer, generating a solid and functional three-dimensional part with reliable mechanical characteristics.
07 – Continuous thermal control
Infrared lamps selectively heat active areas, maintaining the ideal temperature (between 182°C and 186°C) to ensure precise and uniform fusion.
08 – Repeating the cycle
The process is iterated until the part is fully formed. The finished part features high dimensional accuracy, excellent surface quality and consistent mechanical performance, ready for end-use or post-processing
3 print modes for HP Multi Jet Fusion Technology
Each mode is designed to optimize the manufacturing process, allowing you to choose between speed, accuracy, and aesthetic quality based on the specific needs of your project. The different modes keep the mechanical and dimensional properties of the parts unchanged, with differences in print times and final part details.
FAST MODE
Ideal for projects that require speed
production. Perfect for prototypes in a short time.
DIFFERENTIATING FEATURES
- Optimization of printing speed with excellent dimensional accuracy.
MICRONS PER LAYER
- 110 µ
-
Shipping times
Italy: 3, 5, 8 working days | Abroad: 5, 8, 10 working days
BALANCED MODE
Perfect for those who want consistent quality, ideal for functional components and prototypes with finer visual details and improved tactile quality.
DIFFERENTIATING FEATURES
- Optimal balance between dimensional accuracy, accurate detail and aesthetic quality.
MICRONS PER LAYER
- 80 µ
-
Shipping times
Italy: 3, 5, 8 working days | Abroad: 5, 8, 10 working days
ADVANCED MODE
Suitable for high-quality productions that require high visual and tactile accuracy, as well as optimal repeatability for high-value prototypes or final parts.
DIFFERENTIATING FEATURES
- Excellent dimensional accuracy, refined details and superior aesthetic performance.
MICRONS PER LAYER
- 80 µ
-
Shipping times
Italy: 3, 5, 8 working days | Abroad: 5, 8, 10 working days
Versatile Applications of MJF 3D Printing
Solutions for a wide range of industries, all with superior precision and functionality
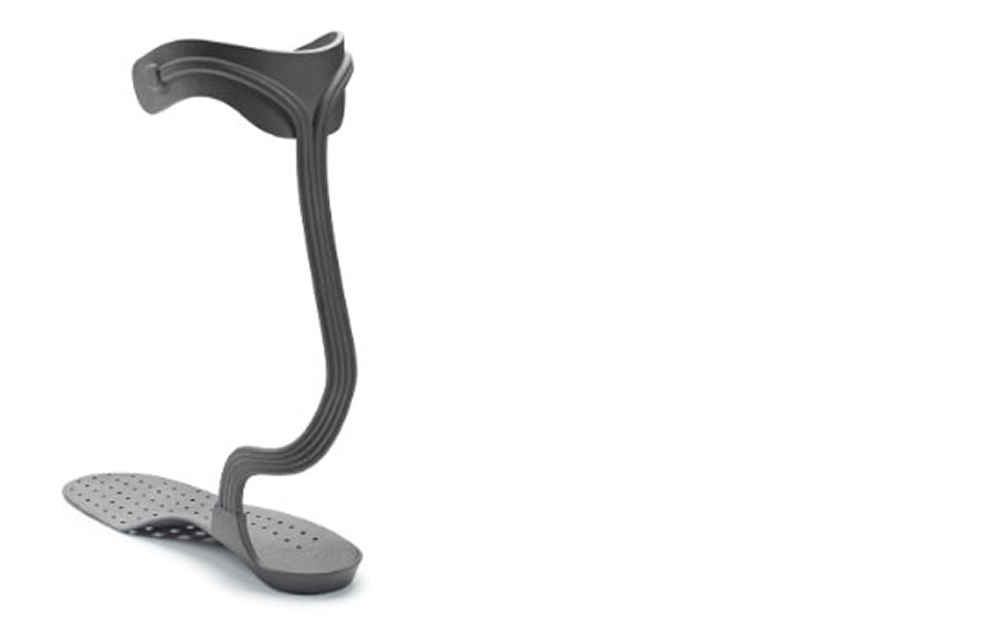
PROTECTIONS
Creation of tailor-made cases and protectors with high precision and resistance.
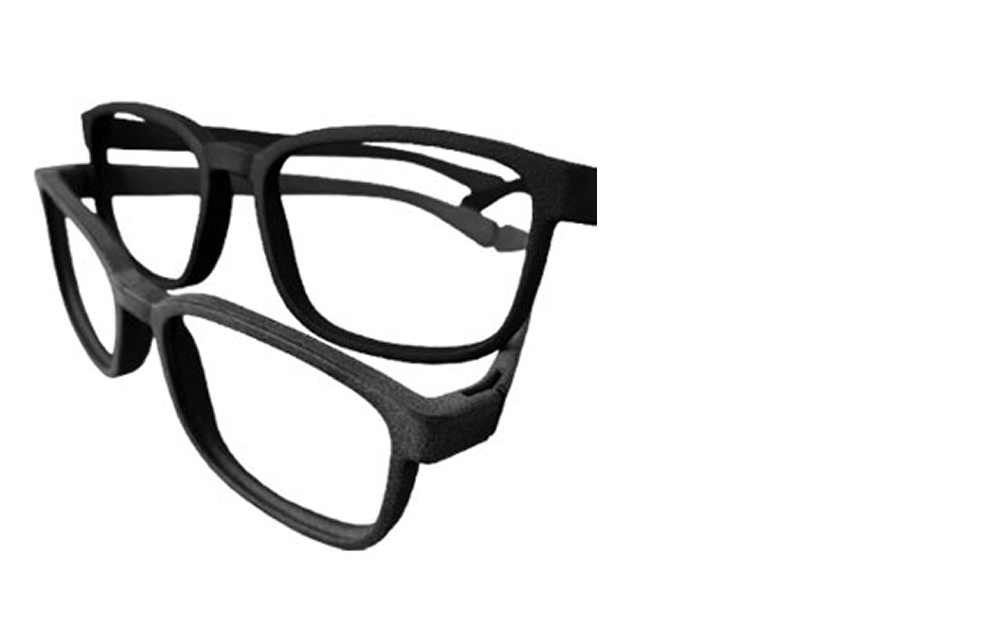
EYEWEAR
Customized, lightweight and durable frames with superior precision and aesthetics.

MECHANICAL PARTS
Manufacture of complex, resistant and functional mechanical components for various sectors.
Optimize your production with HP MJF 3D printing
Are you ready to innovate and optimize your production processes? With HP Multi Jet Fusion technology, we can offer you precise, fast, and highly customizable solutions to meet the unique needs of your business. Contact us to find out how we can help you improve efficiency, quality and production speed.
Why choose HP MJF technology
HP Multi Jet Fusion Technology is the ideal choice for those looking for a balance between quality, speed, and cost.
TRANSPARENT and tailor-made QUOTES
It helps reduce costs with fast printing and the ability to produce multiple parts in a single run, without compromising quality.
PRECISION
MJF printing ensures high dimensional accuracy, with fine details that meet the most complex requirements.
PERFORMANCE
Materials printed with MJF offer excellent mechanical performance, with long-lasting and durable characteristics.
Rapidity
MJF is the ideal solution for rapid prototyping, making it possible to test ideas and designs in a short time and with high precision.
Instant Quote
Process optimization for competitive production
With our online platform, uploading your files and getting a quote is a matter of a few clicks.
Choose the most suitable technology, configure materials, finishes and every technical detail of your request. Receive a instant quote or a custom RFQ and confirm your order in just a few clicks.
You will be able to monitor the progress in real time directly from your reserved area. A fast, transparent and professional production process, without complications.
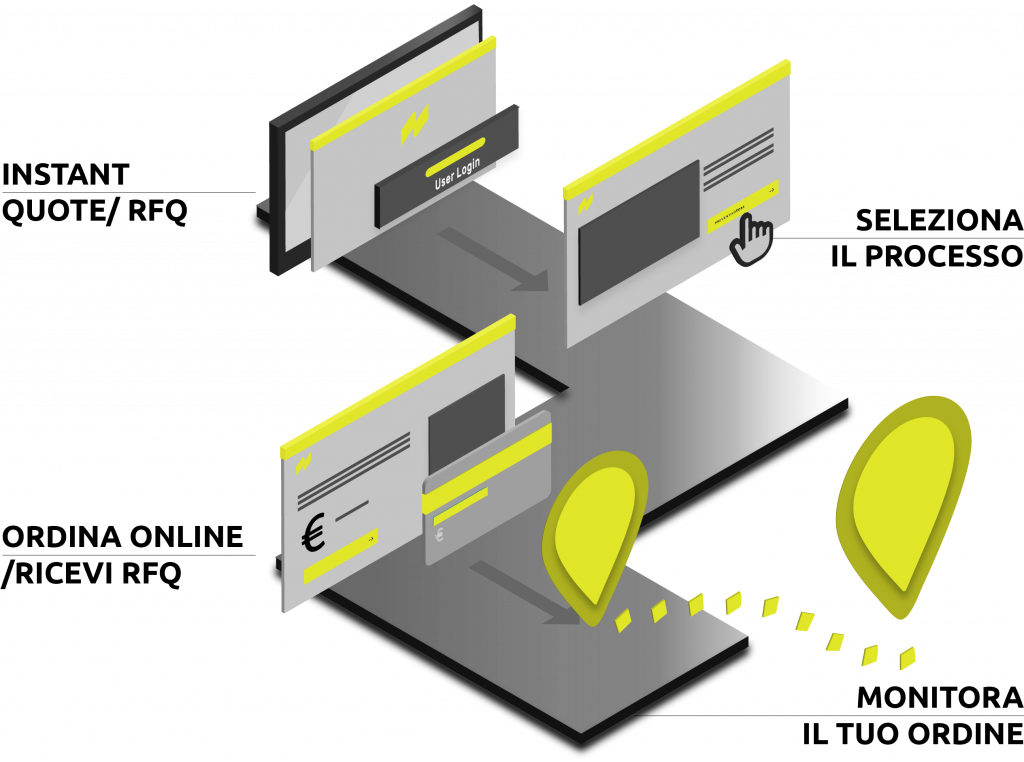
Materials selected to ensure performance and reliability in every application
We offer high-performance materials to meet the different needs of your projects. HP 3D HR PA12, a durable and versatile thermoplastic, is ideal for applications that require high mechanical strength and precision. BASF Ultrasint® TPU01, a thermoplastic elastomer, is designed to offer flexibility, strength and superior performance in dynamic environments.
Materials are fully compatible with HP Multi Jet Fusion technology, ensuring quality and reliability in the most demanding productions.
Post-processing and finishing for parts printed with HP MJF technology
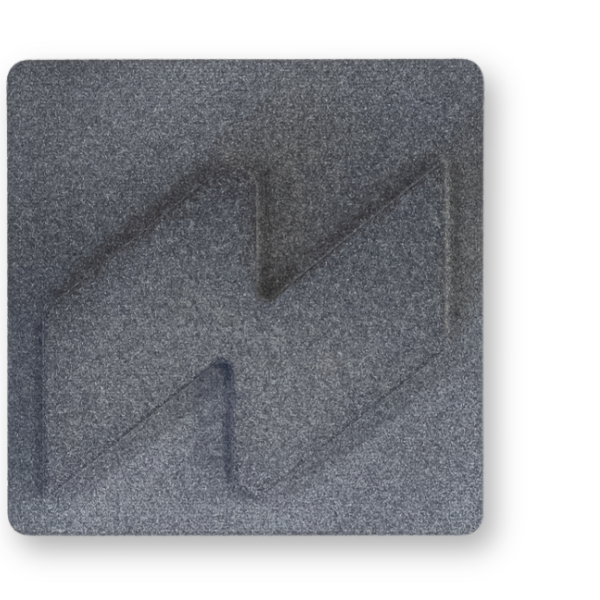
PEENING
In the post-production process of HP-MJF 3D printing, the removal of nylon dust is critical. At Niuo3D, glass micro-spheres (Niuo Micro Glass) are used for effective cleaning and roughness reduction, improving the aesthetics of the product.
- Micro Glass Spheres (Niuo Micro Glass)
- Treatment included for parts manufactured with HP-MJF technology
- Accurate removal of printing surface dust with reduction of surface roughness
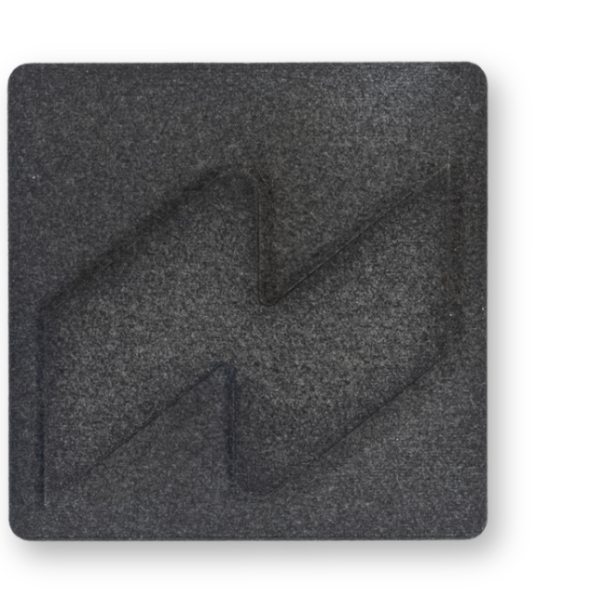
VAPOR SMOOTHING
Advanced post-production process that, through controlled exposure to certified solvent vapors, allows the reduction of the surface roughness of 3D printed parts. The effect obtained in some cases is comparable to that of injection molding.
- Specialized solvents for surface treatment
- Optional treatment at additional cost
- Smoothing of the surface by vaporizing solvents, reducing roughness and closing porosity.
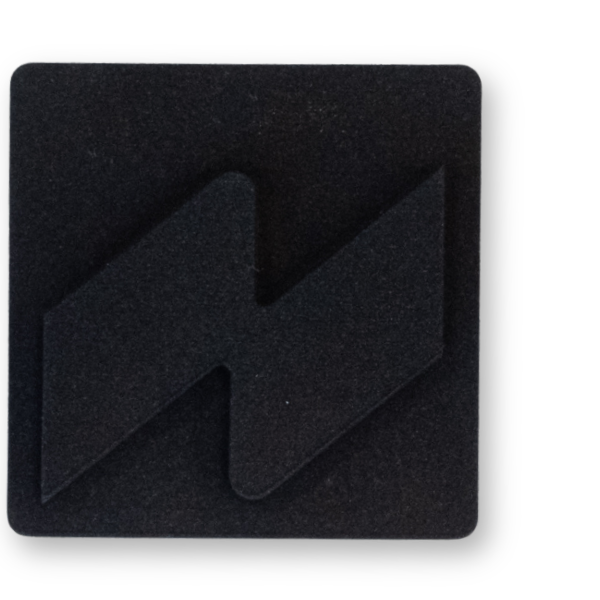
COLOR
Two options are available in the coloring process: TOP BLACK pigmentation for a uniform and durable black, or spray painting with matte or semi-gloss finishes for a personalized and tailored look.
- TOP BLACK pigments or water-based paint
- Optional treatment at additional cost
- Uniform black pigmentation or varnish with matte/semi-gloss options.