Optimize production processes, ensure efficiency and scalability in large volumes.
State-of-the-art technology for series production
Injection molding is the go-to technology for high-volume production of complex plastic components.
Injection molding is a highly functional and cost-effective solution for producing high-level plastic components, ensuring flexibility in managing print runs from medium mass to high volumes.
With Niuo you will have an excellent partner able to meet strict requirements both in terms of structure and aesthetic goals of the part to be made.
With us, you can both purchase the mold and take advantage of our molding services.
Classes of molds for Injection Molding :
The classification of molds according to the Society of Plastics Industry (SPI) ensures quality and durability standards for the injection molding process. Each class is designed to meet specific production needs, balancing strength, precision and production costs.
Class 101
Maximum durability and high-volume production. Molds designed for over 1 million cycles, ideal for continuous production and high-precision components.
DIFFERENTIATING FEATURES
- High-quality stainless steel construction
- High resistance to wear and abrasive agents
- Maximum precision and tight tolerances
- Minimum base hardness: 280 BHN
- High cost, but optimized for large volumes
Class 102
Medium-high production with high strength and precision. Molds for cycles up to 1 million, suitable for medium-high productions and abrasive materials.
DIFFERENTIATING FEATURES
- High-quality steel for durability
- High precision, even for complex geometries
- Mold base with hardness of 280 BHN
- Good wear resistance
- Balancing cost and longevity
Class 103
Versatile solution for moderate productions. Molds with a lifespan of up to 500,000 cycles, ideal for medium-sized productions with low costs.
DIFFERENTIATING FEATURES
- Medium grade steel with a hardness of 165 BHN
- Good accuracy for moderate volumes
- Suitable for less abrasive materials
- Lower costs than higher classes
- Greater flexibility in mold design
Class 104
For low-volume production and low costs. Molds with a lifespan of up to 100,000 cycles, perfect for small batches and prototypes.
DIFFERENTIATING FEATURES
- Less expensive materials: mild steel or aluminum
- Hardness less than 165 BHN
- Adequate accuracy, but not for tight tolerances
- Reduced production time for quick start-up
- Cost-effective, ideal for testing and small series
First Class Mold | Duration [cycles] | Production volume | Mold Material | Hardness [BHN] |
---|---|---|---|---|
101 | + 1 million | High-mass production | High quality steel (stainless steel) | 280 |
102 | up to 1 million | Medium - High | High-quality steel | 280 |
103 | up to 500 thousand | Medium | Medium grade steel | 165 |
104 | up to 100 thousand | Contents | Mild steel or aluminum alloys | < 165 |
Online quotation
Request a quick and personalized quote through our RFQ system dedicated to injection molding.
Upload your files, select the desired materials and finishes, and send your request to receive a detailed quote.
Make sure that all component specifications are clearly stated in the uploaded files. You will be able to monitor the entire process directly from your account, enjoying a completely digital, transparent and efficient experience.
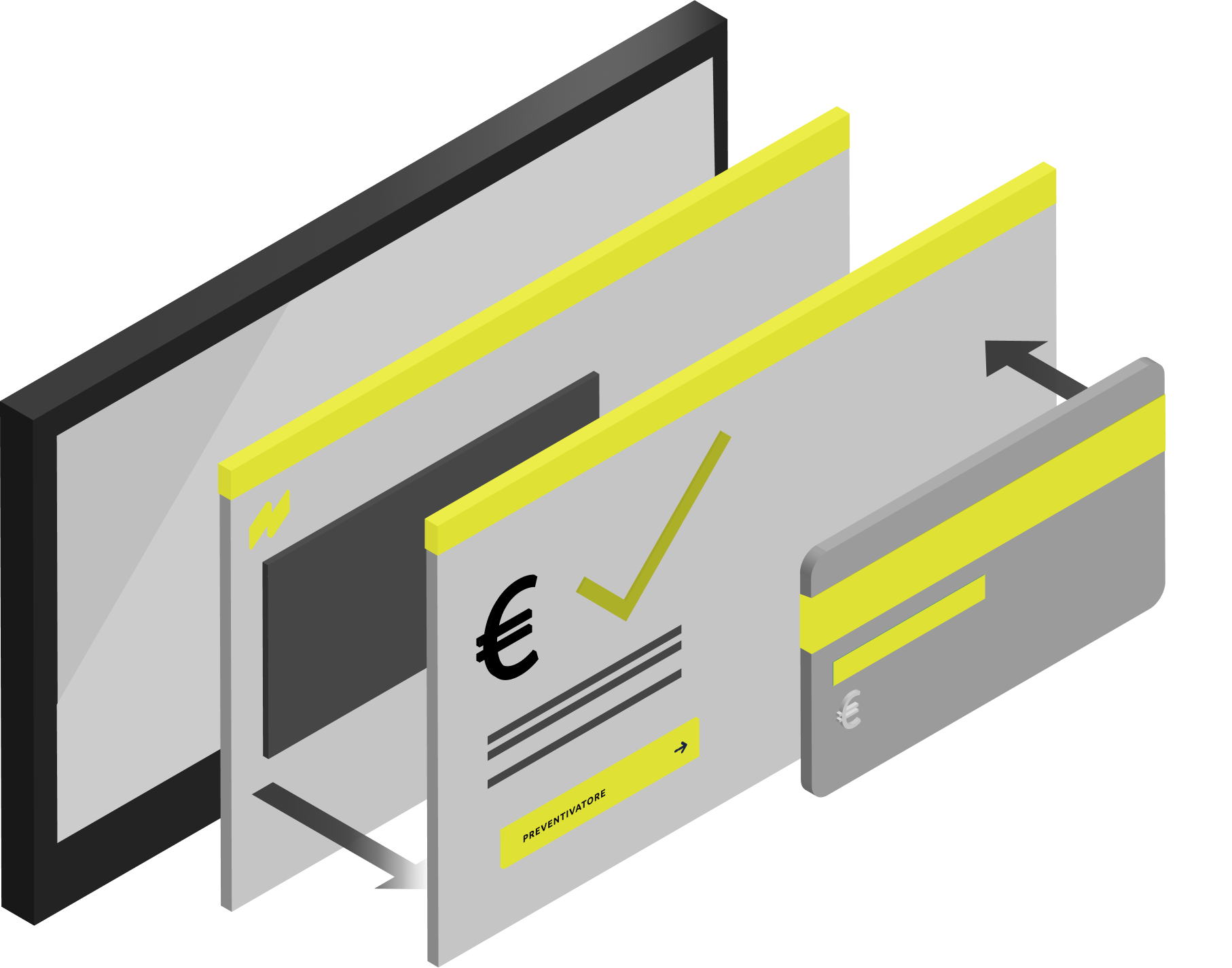
QUICK management
Upon receipt of your request, a team of specialists in the injection molding sector will immediately carry out the analysis of the part to be made, providing rapid feedback on times and costs, including separate indications between the price necessary for the mold and the cost of the part based on the required runs.
MAXIMUM PRECISION
Thanks to advanced technologies and high-precision moulding processes, we offer proofs according to the ISO 16742 standard, depending on the precision required on the mould and the sizing of the parts.
MATERIAL SELECTION
We offer a wide selection of materials, allowing you to choose the most suitable ones to obtain the desired strength, durability and surface quality, based on the specific needs of each production.
SERIES PRODUCTION
By optimizing the injection molding process, we can ensure fast, efficient and high-quality series production for large volumes at competitive costs, excluding the fixed costs associated with mold creation.
Components can be ordered starting from 150 pieces.
MOLD COMPONENTS
Thanks to the consolidated collaboration with our partner specialized in injection molding and the production of technical components for this process, at Niuo you will have the opportunity to request single, family or multi-cavity molds.
EXCELLENT QUALITY
We believe that the foundation of every project lies in paying the utmost attention to all planned work phases, starting from the preliminary analysis, but especially to the quality control defined for production batches and finished parts.
Thanks to a highly qualified structure and oversight of the post-production phases, at Niuo we pride ourselves on having a key element to consistently offer items that fully meet the reference standards required by the customer.
Need to get expert support?
Our dedicated team is at your disposal to guide you in choosing the most suitable solution for your project. Contact us for more information.
Choosing Niuo as a strategic partner for injection molding processes means:
- Obtaining plastic components made only through the use of the best innovative technologies;
- Access to machining with insert molding;
- To create components and parts through overmolding processes;
- Having the option to choose different types of moulds: single, family and multi-cavity;
- Accessing a wide range of materials;
- Applying top-quality surface finishes to the parts;
- Entrusting the preliminary feasibility analysis to a highly specialized team;
- Construction times communicated during the quotation phase, transparent and respected;
- Make molds with excellent accuracy and precision.
High precision, speed and quality for large-scale industrial production
High Accuracy and Repeatability
Injection molding enables the production of components with extremely tight tolerances, ensuring maximum precision and consistency in production runs, even for large volume batches.
High production efficiency
Thanks to fast and automated production cycles, this technology makes it possible to reduce production times and optimize the use of resources, while keeping costs low for series production.
Versatility in
Materials
The wide range of materials, including thermoplastics, rubber, and reinforced materials, makes injection molding suitable for a wide variety of industrial applications in various sectors and industries.
Superior Quality and Control
The specialized expertise of the team employed, combined with the strategic partnership with a leading company, guarantee strict control and superior quality at every stage of the process.
Compatible materials for every industrial need
Rigid plastics, elastomers and synthetic rubbers, a wide range of materials to meet the technical and functional specifications of every industrial sector.
Finishes for injection molding:
SPI Surface Finishes
These finishes determine the final appearance of the component, improving both aesthetic and functional qualities, depending on the type of surface desired. The SPI classification is divided into four main categories, ranging from maximum gloss to more matte and structured finishes, adaptable to design and performance needs.
- Category A: Mirror Polishing – Maximum brilliance, ideal for visible components.
- Category B: Semi-polishing – Moderate gloss, suitable for industrial applications.
- Category C: Matte Finish – Glare-free surface, reduces glare.
- Category D: Satin Texture – Specific textures for functional and decorative applications.
- Each category includes several subcategories that determine the degree of polish or texture.
VDI Surface Finishes
The VDI numeric scale indicates the roughness of the surface, from smooth to rough, with lower numbers corresponding to smoother finishes and higher numbers to rougher surfaces, ideal for industrial applications that require specific functionality. This system is essential to adapt the surface to the technical and aesthetic requirements of each project.
- VDI 12: Very smooth surface with minimal roughness, ideal for aesthetic components.
- VDI 15-21: Light to medium roughness, for applications that require functionality combined with aesthetics.
- VDI 24-33: Surfaces with increased roughness, suitable for technical and industrial applications.
- VDI 36-45: Rough surface, used for components that need wear resistance or anti-slip properties.
- The choice of finish depends on the aesthetic and functional needs of the final product.
Frequently asked questions
RFQ Quote: Get a detailed quote for machining, services, and finishes.
What are the differences between SPI mold classes?
The Society of Plastics Industry (SPI) mold classes are standardized based on durability and manufacturing materials:
- Class 101: Suitable for mass production with more than 1 million cycles, made of high-quality steel.
- Class 102: For medium to high volumes, up to 1 million cycles, suitable for applications requiring high precision.
- Class 103: For medium volumes, up to 500,000 cycles, made of medium quality steel.
- Class 104: For low-volume production, up to 100,000 cycles, made of mild steel or aluminum alloys.
What materials can I choose for my injection molding project?
We offer a wide range of materials to meet different needs for strength, durability and surface properties. The main materials include thermoplastic polymers such as ABS, PC, and PA, as well as high-performance materials such as PEEK and PEI, which are ideal for applications that require resistance to high temperatures or extreme conditions.
What kind of surface finishes can I choose for my molded components?
We offer two main types of finishes:
- SPI finishes: Including glossy, semi-gloss, matte and sandblasted finishes. Each category (A, B, C, D) offers different options to meet specific aesthetic and functional needs.
- VDI finishes: A numerical scale ranging from smooth (VDI 12) to rougher (VDI 45) finish, ideal for applications that require anti-slip properties or wear-resistant surfaces.
How do I get a quote for injection molding?
You can easily request a quote using our online RFQ system. Simply upload your project files, select the desired materials and finishes, and submit your request. You’ll receive a personalized quote in just a few steps, with the option to track progress directly from your account.