Apply finishes to your products that combine durability, aesthetics and performance.
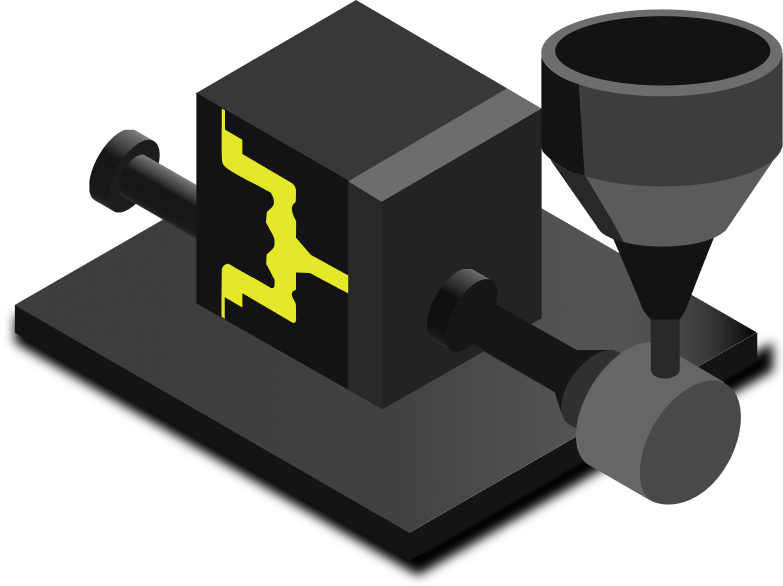
SPI Surface Finishes for Injection Molded Parts
The Society of the Plastics Industry (SPI) finishes are an international standard for the classification of injection molding surfaces.
These finishesdetermine the final appearance of the moulded part and can influence its functionality and aesthetics. SPI finishes are divided into four main categories, each with different subcategories that are distinguished by the level of polish and texture obtained.
SPI finishes offer a diverse range of options to suit customers’ aesthetic and functional needs. The choice of the appropriate finish depends on the specific requirements of the final product, ensuring high quality and optimal results every time.
Category A: Mirror polishing
Category A stands for maximum gloss and mirrored finish. This type of finish is ideal for applications where aesthetic appearance is crucial, such as in the visible components of consumer products.
SUBCATEGORIES
- A-1: The highest finish, obtained with ultra-fine diamond pastes, gives a surface free of visible imperfections.
- A-2: High-gloss polishing, obtained with fine diamond pastes, but slightly lower than A-1 in terms of reflectivity.
- A-3: Standard mirror polishing, obtained with medium-grit diamond pastes, which still offers a high gloss but with a lower level of detail than A-1 and A-2.
ADVANTAGES
- Benefits include exceptional gloss and a mirrored appearance, perfect for aesthetic applications where reflection and gloss are critical.
Category B: Semi-Polishing
Category B offers less intense polishing than category A, resulting in smooth surfaces but with attenuated reflections.
SUBCATEGORIES
- B-1: Fine semi-polishing, obtained with alumina-based abrasives, which guarantees a smooth and uniform surface with a slight shine.
- B-2: Medium semi-polish, achieved with medium grit abrasives, ideal for applications where attenuated reflection is desired.
- B-3: Coarse semi-polishing, achieved with coarse-grained abrasives, providing a smooth surface but with even less gloss.
ADVANTAGES
- Benefits include a smooth finish and muted highlights, ideal for applications where gloss is important but not predominant.
Category C: Matte Finish
Category C is designed to achieve matte surfaces with minimal reflection. This category is often used in applications where glare reduction is essential.
SUBCATEGORIES
- C-1: Fine matting, achieved with silicon carbide abrasives, which produces a uniform surface with moderate opacity.
- C-2: Medium opacity, achieved with medium grit abrasives, which provides a more pronounced opacity.
- C-3: Coarse matting, achieved with coarse-grained abrasives, which produces a rough surface with high opacity.
ADVANTAGES
- Benefits include reduced glare and matte surfaces, perfect for applications where reduced visibility is required without compromising on functionality.
Category D: Satin Texture
Category D focuses on satin surfaces with specific textures, suitable for decorative or functional applications.
SUBCATEGORIES
- D-1: A fine texture, obtained by sandblasting or other light abrasive techniques, which gives a fine and uniform satin texture.
- D-2: Medium texture, obtained with medium grain abrasive techniques, which offers a more pronounced satin texture.
- D-3: Coarse texture, obtained with coarse-grained abrasive techniques, which provides a noticeable and marked satin texture.
ADVANTAGES
- Benefits include a satin and durable texture, which provides a sleek and functional look, suitable for decorative and practical applications.
VDI surface finishes for injection molded parts
VDI (Verein Deutscher Ingenieure) finishes are a standard, mainly adopted in the German industrial market, used to classify the surfaces of parts obtained by injection molding.
This standard is essential for determining the final appearance of the part and for meeting specific aesthetic and functional requirements. VDI finishes are categorized through a numerical scale that indicates the degree of roughness of the surface, with lower numbers representing smoother surfaces and higher numbers representing rougher surfaces.
VDI 12
This finish offers a very smooth surface with minimal roughness. It is achieved by fine polishing, often using very fine-grained abrasives or special polishing pastes. It is ideal for applications where high esthetics and a high surface area are required.
FEATURES
- Very smooth surface with minimal roughness
- finely polished with fine-grained abrasives.
ADVANTAGES
- Benefits include a high aesthetic appearance, with a reflective surface that is ideal for design or visible applications.
VDI 15
With a slight roughness compared to VDI 12, this finish is achieved with slightly coarser grain abrasives. It provides a smooth surface, but with a slight texture that can improve the grip or adhesion of paints.
FEATURES
- Smooth surface with light texture
- Polishing with coarser grain abrasives.
ADVANTAGES
- Benefits include a surface with better adhesion for paints and a lightness in improving grip without compromising aesthetics.
VDI 18
The roughness increases slightly compared to VDI 15. This level is often achieved through a light sandblasting process, which gives the surface a uniform and tactile texture . It is suitable for applications that require a balance between aesthetics and tactile functionality.
FEATURES
- Slight roughness
- Uniform texture
ADVANTAGES
- Benefits include a perfect balance between aesthetics and functionality, ideal for components that require a good compromise between visibility and usability.
VDI 21
This finish has a moderate roughness, obtained by sandblasting with medium-grit abrasives. The surface is visibly textured, which can be useful for applications where more grip is required or to hide imperfections.
FEATURES
- Moderate roughness
- Sandblasting with medium-grit abrasives
ADVANTAGES
- Benefits include increased grip and the ability to hide imperfections, which is useful for practical and functional applications.
VDI 24
The roughness is more pronounced, obtained through more intense abrasive processes. The surface is distinctly textured, ideal for industrial applications or where a non-slip surface is required.
FEATURES
- Pronounced roughness
- Sandblasting with coarse-grained abrasives
ADVANTAGES
- Benefits include a non-slip surface, ideal for industrial applications that require robustness and functionality.
VDI 27
With an even greater roughness, this finish is often used for industrial or technical components where functionality exceeds aesthetics. It is obtained by intense sandblasting or surface incisions.
FEATURES
- High roughness
- Intense sandblasting or surface engraving
ADVANTAGES
- Advantages include high technical functionality, suitable for components that require strength at the expense of aesthetics.
VDI 30
This finish offers a rough surface, obtained with very coarse abrasives or heavy blasting techniques. It is mainly used for applications where it is crucial to avoid slipping or to improve grip.
FEATURES
- Rough surface
- Heavy blasting with coarse abrasives
ADVANTAGES
- Benefits include a high-wear-resistant, non-slip surface, ideal for applications that require a secure grip.
VDI 33
It has avery evident roughness, created through intensive abrasive processes. The texture is visibly pronounced, ideal for components that require a robust and durable surface.
FEATURES
- Noticeable roughness
- Intensive abrasives
ADVANTAGES
- Benefits include increased strength and durability, perfect for applications that require a long service life and durability.
VDI 36
The surface is extremely rough, obtained through very aggressive abrasive techniques. It is suitable for specific technical applications that require high wear resistance.
FEATURES
- Extreme roughness
- Aggressive abrasives
ADVANTAGES
- Advantages include high wear resistance, which is ideal for components in particularly harsh environments.
VDI 39
This finish has a very high roughness, achieved by sandblasting with very coarse abrasives. It is used for technical pieces where rough texture is needed for functional reasons.
FEATURES
- High roughness
- Sandblasting with coarse abrasives
ADVANTAGES
- Benefits include an extremely durable surface, ideal for functional applications that require hardness and strength.
VDI 42
With an extremely high roughness, this finish is used in highly technical applications. The rough surface is obtained through intense and repeated abrasive processes.
FEATURES
- Very high roughness
- Intense and repeated abrasives
ADVANTAGES
- Benefits include a durable and robust surface, perfect for industrial environments that need high strength.
VDI 45
The roughest VDI finish, achieved through extremely aggressive abrasive processes. The texture is very pronounced, ideal for components that require maximum wear resistance and a non-slip surface.
FEATURES
- Maximum roughness
- Extremely aggressive abrasives
ADVANTAGES
- Benefits include maximum wear resistance and non-slip surface, perfect for extreme environment applications.