Get a custom quote: upload files and select specifications
Tight tolerances and precision with advanced 5-axis CNC milling and turning technologies
CNC turning and milling: choose the ideal technology for your machining
CNC Turning
Machining technique that allows the production of cylindrical parts with extremely precise tolerances, using numerical control machines. Perfect for making components with symmetrical shapes.
PARAMETERS
- Ø min 6
- Ø max 550
- Max length 800
ADVANTAGES
- High precision in cylindrical machining
- Advanced CNC machinery for complex machining
- Superior finishes with tight tolerances
- The use of a CNC lathe makes it possible to create complex geometries and ensure micrometric precision, even on difficult materials.
CNC Milling
A machining technique that allows material to be removed by means of a rotary cutter. Ideal for producing components with complex shapes, precise angles and perfect surfaces.
PARAMETERS
- X max 2600
- Y max 1100
- Z max 950
ADVANTAGES
- High versatility in complex geometries
- Millesimal precision on materials of various hardness
- Wide range of machinable materials
- The use of 5-axis CNC milling allows for more complex machining in a single step, reducing production time.
Online quotation
Request an online quote in a few steps
Log in to our platform and get a custom quote for your CNC machining. Upload your files, choose the desired technology, materials and finishes, and submit your request, our team of experts normally takes 48h from the moment an RFQ request is made.
You can follow the progress of the project directly from your account. A simple, fast and transparent process, for production without surprises.
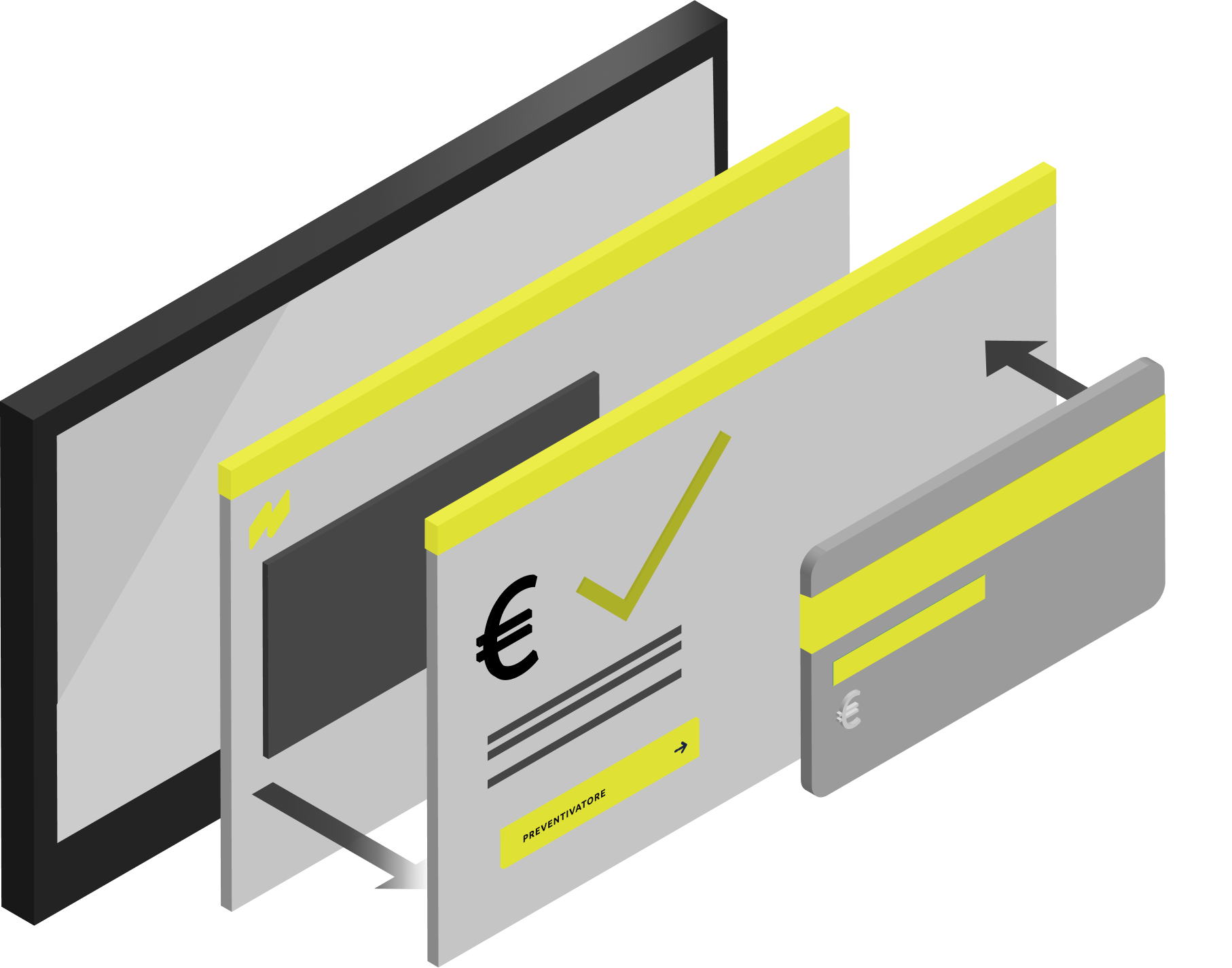
OPTIMIZED PROCESSES
We manage the production of welded assemblies using advanced technologies and optimized workflows, integrating 5-axis CNC machining, turning and milling. Reducing time, costs and margins of error, ensuring high-precision results even on advanced industrial projects.
RAPID PROTOTYPING
We create prototypes in a short time, guaranteeing high precision and quality. A service designed to optimize the verification, adaptation and optimization phases of the project, before the final production, ensuring a final result perfectly in line with the required specifications.
HIGH PERFORMANCE
We carry out tailor-made CNC machining, designed to guarantee dimensional accuracy, reliability and high performance even in the most complex applications. We offer a complete service, from the processing of the individual components to the final integration, compliance with the required specifications.
PRODUCTION TECHNOLOGIES
CNC turning and milling machining is at the heart of our production, offering versatile and high-precision solutions. Thanks to advanced technologies and accurate control of each step, we produce components that are reliable, precise and ready to be integrated into complex systems.
Advanced 5-axis CNC machining: precision, flexibility and support for every industrial need
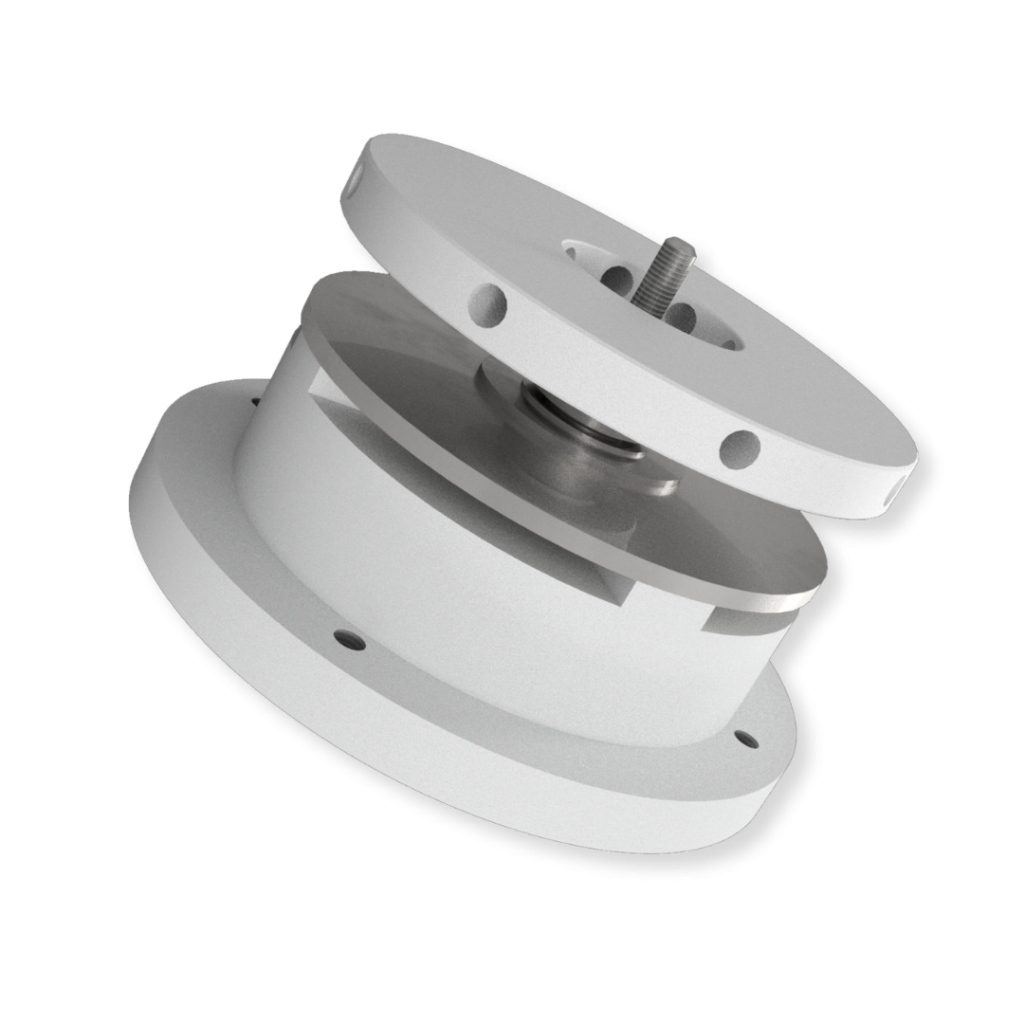
Precision and Tight Tolerances
Our CNC machining guarantees high dimensional accuracy and tight tolerances, thanks to the use of state-of-the-art machining centers. Each component is made with accurate control, ensuring reliability and repeatability, even on complex geometries.
Customized
Production
We offer completely tailor-made solutions, adapting technologies and materials according to the technical specifications provided by the customer. We efficiently manage both one-off prototypes and mass production, maintaining consistency and quality in every batch.
Operational efficiency and reliable lead times
Each phase of the production process is organized to maximize efficiency: we reduce tooling times, minimize rework and optimize order management. This allows us to guarantee fast and reliable delivery times, even for complex or urgent orders.
SPECIALIZED TECHNICAL CONSULTANCY
Our technical team supports the customer in all phases: from the evaluation of the design, to the choice of materials and the definition of the most suitable processing parameters. Concrete support to transform every project into a perfectly compliant component
Not sure which technology is the most suitable?
Our dedicated team is at your disposal to guide you in choosing the most suitable solution for your project. Contact us for more information.
Learn more about CNC technologies for your production
Find out how our advanced solutions can optimize your production processes. The CNC technologies we use are state-of-the-art and guarantee precision, efficiency and versatility.
With our service, you will be able to access customized solutions for every type of processing, taking advantage of the latest generation machinery and optimized processes to reduce production times without compromising quality.
Take advantage of our online quote to receive a quick and detailed quote, normally within 48 hours from the moment you receive an RFQ. In addition, our team of experts is always available for targeted advice, helping you choose the technology that best suits your specific needs.
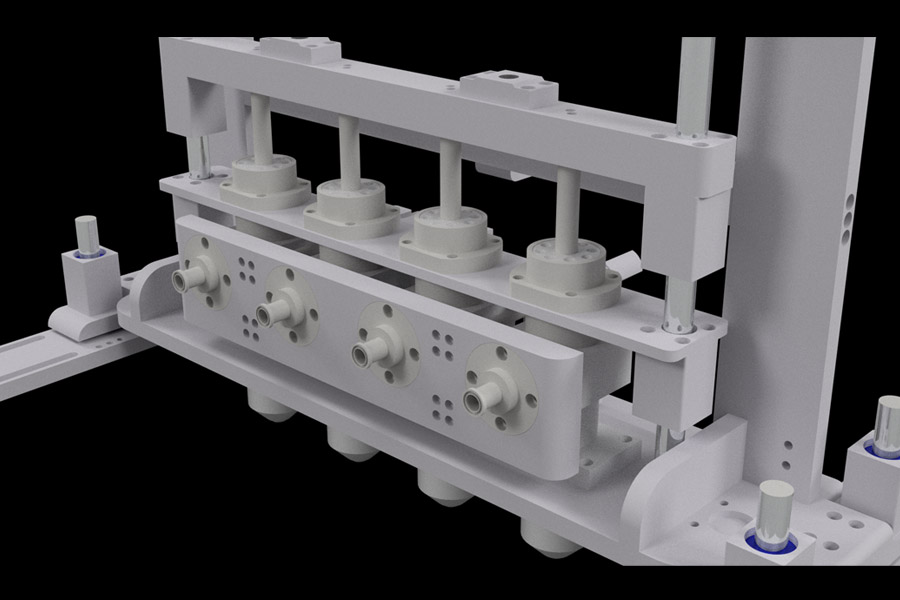
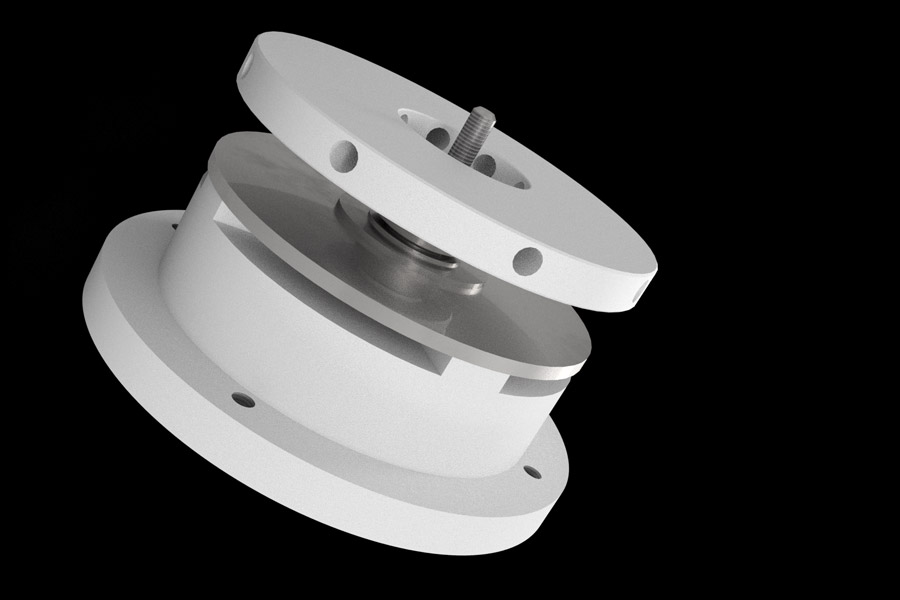
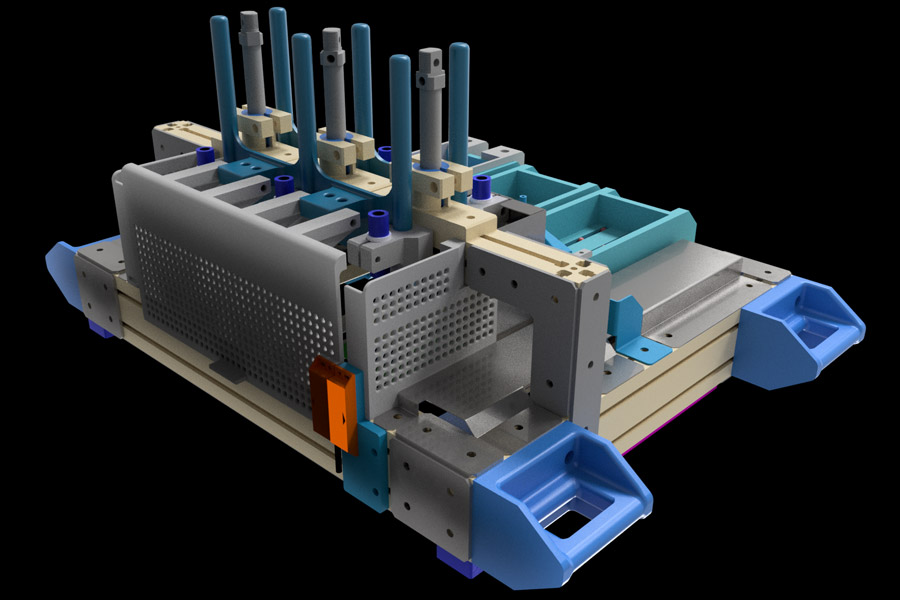
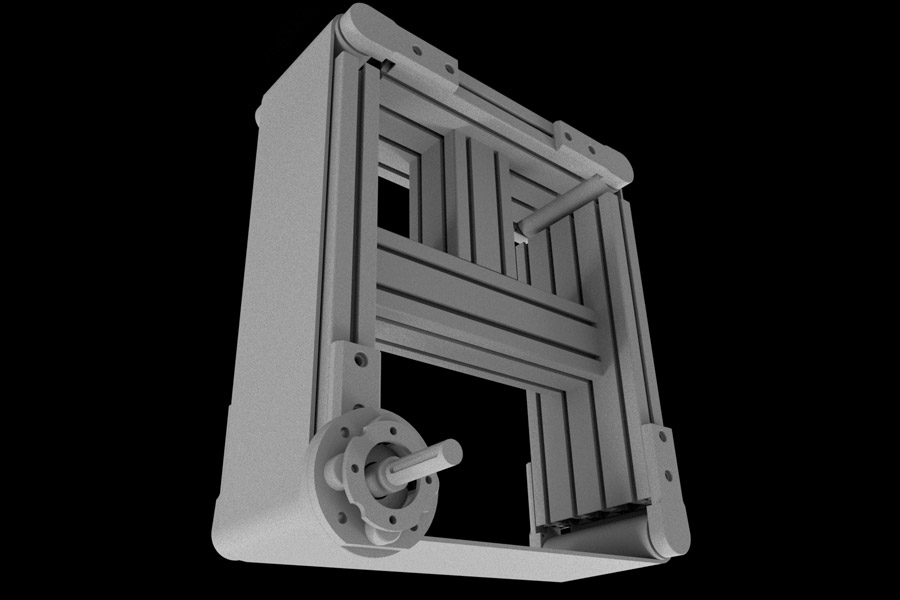
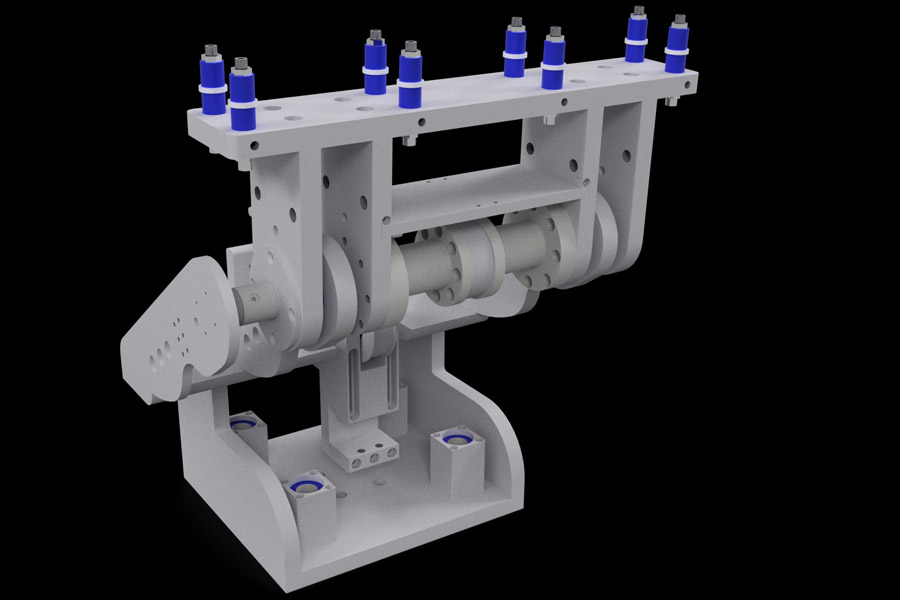
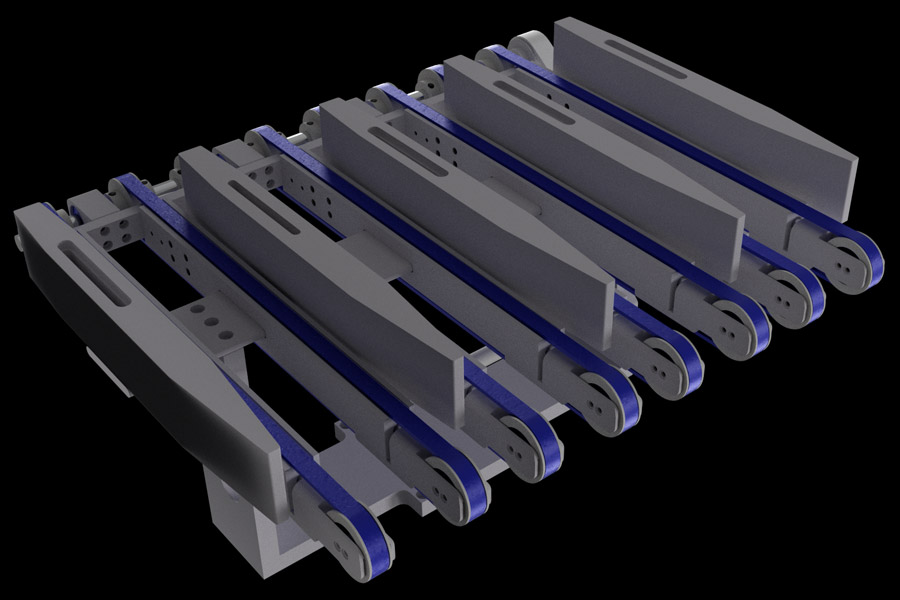
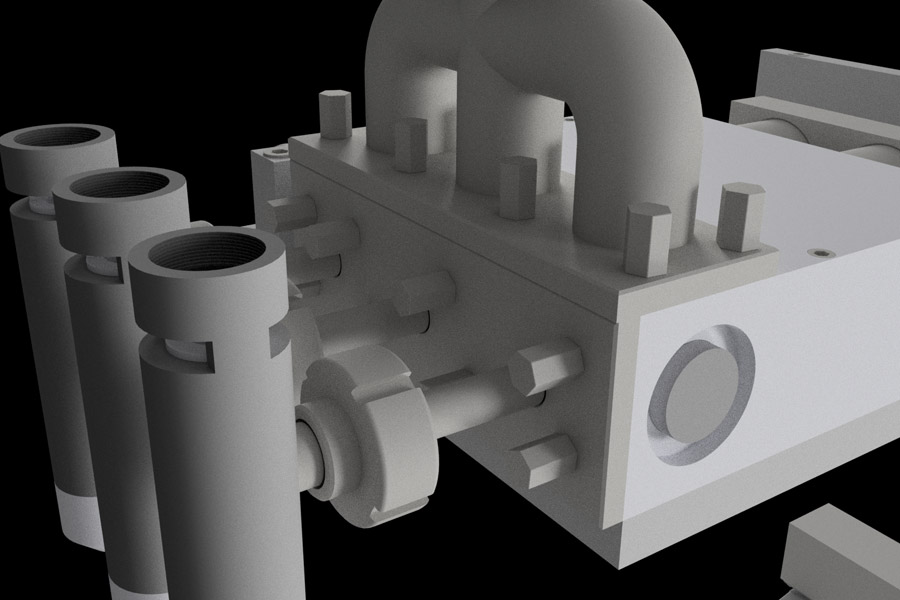
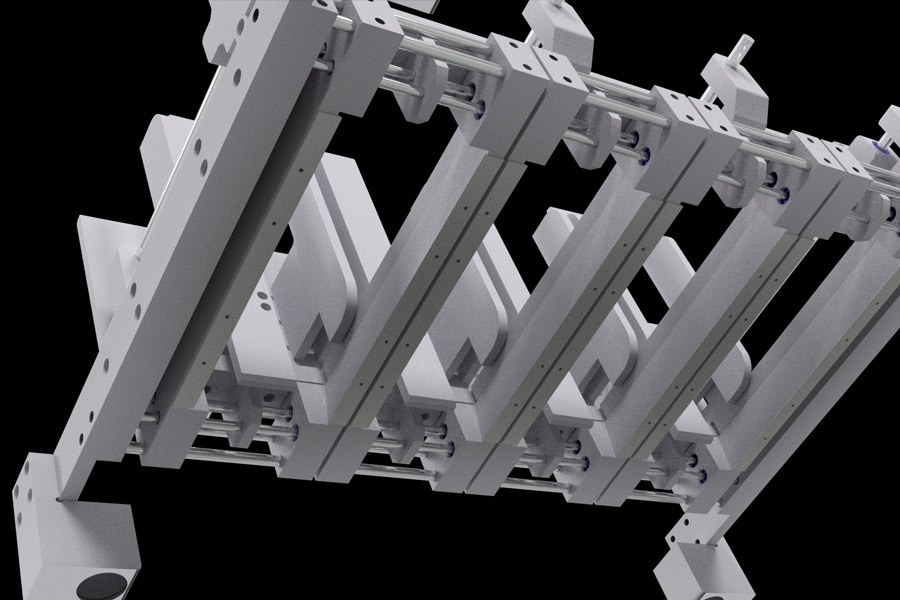
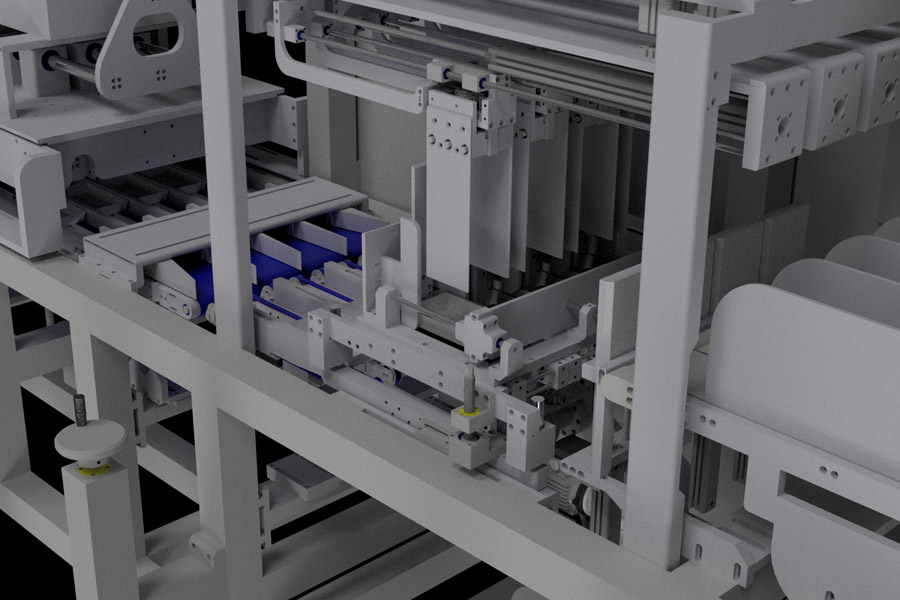
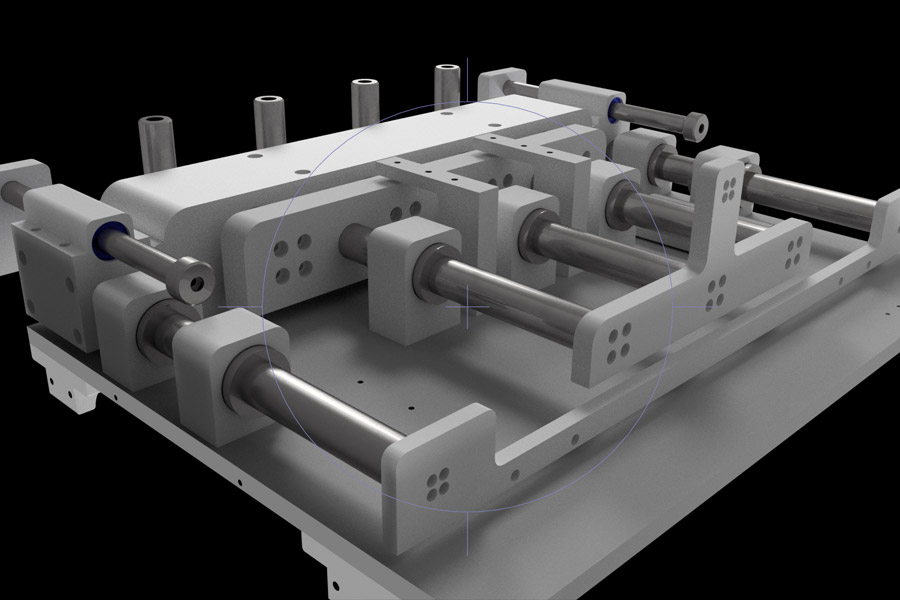
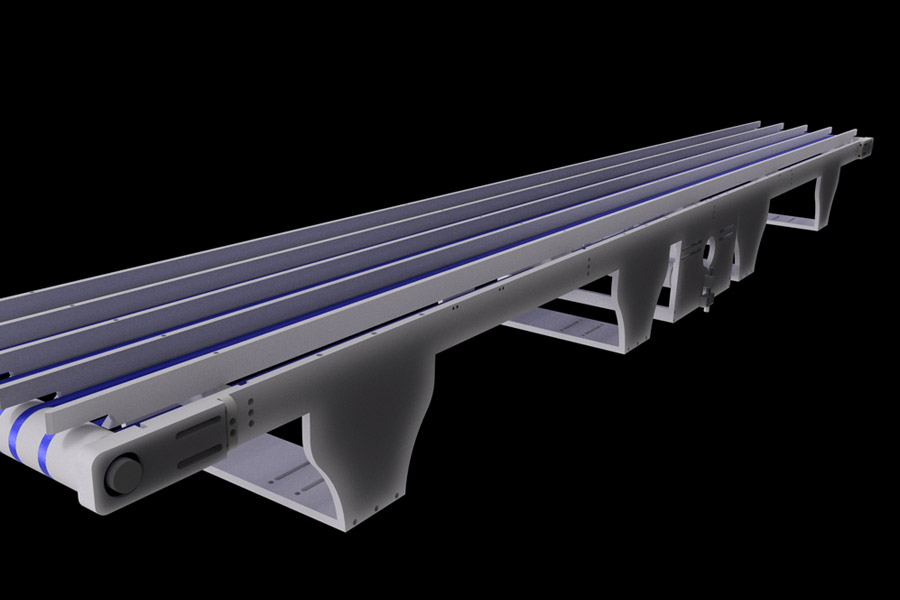
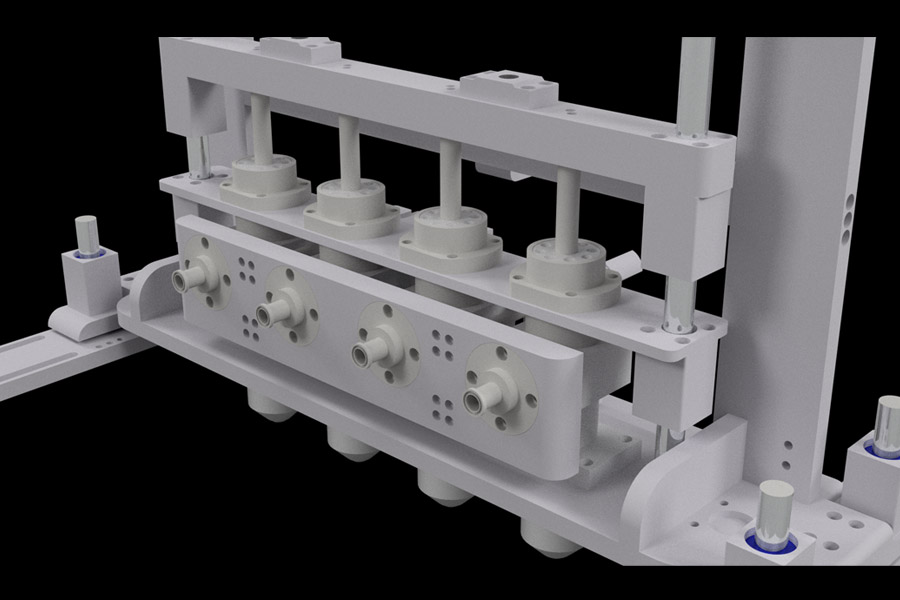
5-axis CNC machining: maximum precision and production flexibility.
EXTREME
PRECISION
At Niuo, precision is not an achievement, but a standard. Thanks to high-tech CNC machining centers and rigorously controlled production processes, we produce components with minimum tolerances and absolute repeatability, even on complex geometries. Each phase is monitored to ensure total compliance with technical specifications, with accurate dimensional control on each piece produced.
Flexibility in geometries
Our CNC machining, especially 5-axis milling, allows the realization of complex shapes, multiple curves and multi-sided machining in a single setup.
This ability allows us to tackle challenging projects without compromising on precision or time, offering the customer maximum design freedom, even for mass production.
Repeatability and consistency
Niuo guarantees consistency and reliability in every single piece produced. Whether it’s one-off batches or serial production, we ensure consistent quality standards thanks to highly stable CNC machines, optimized cycles and in-process controls. Each component is the same as the previous one, with guaranteed repeatability that makes our process ideal even for highly critical applications.
Efficiency and time optimization
We have designed every step of our CNC production flow to be lean, responsive and reliable. Thanks to the integration of CAM programming, rapid setup and internal order management, we minimize setup times and maximize yield. The result? Reduced production times, punctual deliveries and efficient handling even for complex and urgent orders.
Precision, versatility and performance: CNC machining for industrial components
CNC machining represents a highly reliable solution for the production of precision mechanical components, both for prototypes and for small to medium production series. This technology allows to operate on a wide variety of materials, including stainless steel, aluminum, titanium and engineering plastics, offering excellent results in terms of dimensional accuracy, stability and repeatability.
Thanks to the mechanical and thermal characteristics of the processed materials, CNC is particularly suitable for the production of structural parts, functional elements and components intended for complex or stressed operating environments. The process also allows for advanced customization, rapid prototyping and a high-quality surface finish.
To complement this, we offer a range of post-process processes such as threading, heat and surface treatments, anodizing, painting and much more, to deliver finished and ready-to-integrate components, meeting the most demanding industry standards. Precision, versatility and performance: CNC machining for industrial components.
CNC machining represents a highly reliable solution for the production of precision mechanical components, both in the prototype field and for small and medium series. This technology allows it to operate on a wide variety of materials, including stainless steel, aluminum, titanium and engineering plastics, offering excellent results in terms of dimensional accuracy, stability and repeatability.
Thanks to the mechanical and thermal characteristics of the processed materials, CNC is particularly suitable for the production of structural parts, functional elements and components intended for complex or stressed operating environments. The process also allows for advanced customization, rapid prototyping and a high-quality surface finish.
To complement this, we offer a range of post-process processes such as threading, heat and surface treatments, anodizing, painting and much more, to deliver finished and ready-to-integrate components, meeting the most demanding industry standards.
Materials compatible with CNC technology
Discover how our machining technology can transform a wide range of materials, from aluminum to titanium, to achieve high-precision and high-performance results.
Post-processing and finishing for parts made with CNC machining
Anodization
Anodizing is an electrochemical process that improves corrosion resistance and gives an aesthetic and durable surface.
- Increases corrosion resistance.
- Red, blue, black and transparent coloring.
- It gives a decorative surface.
- Improves material durability.
- Protects against atmospheric factors.
Polishing
Polishing is a process that improves the appearance and surface quality, giving metals a smooth and shiny finish.
- Eliminates surface imperfections.
- It makes the surface smooth and shiny.
- Increases corrosion resistance.
- Facilitates cleaning and maintenance.
- It gives a professional look.
Electropolishing
It improves the surface of metals through an electrochemical process, increasing gloss and corrosion resistance.
- Reduces surface roughness.
- Increases the shine of the material.
- Improves corrosion resistance.
- Facilitates cleaning and maintenance.
- Reduces surface contamination.
Burnishing
Burnishing gives a dark and uniform finish, protecting the material from atmospheric agents and improving durability.
- It gives a sleek and uniform look.
- Increases corrosion resistance.
- Reduces friction and wear.
- Improves material durability.
- Protects against atmospheric agents.
Chromium plating
It applies a layer of chromium to metals, giving a glossy finish and increasing resistance to corrosion and wear.
- It gives a shiny and shiny surface.
- Increases corrosion resistance.
- Improves material durability.
- Protects against atmospheric and chemical agents.
- Increases the hardness of the surface.
Electroless nickel plating
Electroless nickel plating deposits an even layer of nickel on metal surfaces, improving durability and aesthetic appeal.
- Uniform coverage on complex surfaces.
- Improves corrosion resistance.
- Increases surface hardness.
- It gives shine and durability.
- Great for complex geometries.
Peening
Shot peening uses small abrasive balls to improve fatigue resistance and material life, giving it a uniform finish.
- Increases fatigue resistance
- Provides a uniform finish.
- Removes surface imperfections.
- Extends the lifespan of the component
- Facilitates the maintenance of materials.
Cataphoresis painting
Cataphoresis coating provides strong, consistent protection that is ideal for complex metal surfaces.
- Uniform coverage.
- Increases corrosion resistance.
- Reduces maintenance costs.
- Offers a durable and long-lasting finish.
- Protects against atmospheric agents.
Powder coating
Powder coating creates a uniform and durable finish, which is ideal for protecting the material from weather and physical damage.
- Creates a uniform finish without dripping.
- Increases corrosion resistance.
- It does not use solvents.
- Resistant to physical damage and abrasion.
- It gives a uniform aesthetic appearance.
Zincification
Galvanizing applies a protective layer of zinc, protecting metals from corrosion and increasing their durability.
- Protects against rust and corrosion.
- Increases the durability of the material.
- Improves aesthetic properties.
- Facilitates cleaning and maintenance.
- Protects against atmospheric and chemical agents.
Passivation
Passivation improves corrosion resistance by creating a protective layer of chromium oxide.
- Increases corrosion resistance.
- Prevents rust from forming.
- Improves the durability of the material.
- Protects against atmospheric agents.
- Increases the service life of the material.
Frequently asked questions
RFQ Quote: Get a detailed quote for machining, services, and finishes.
What are the tolerances that can be applied to CNC machining?
Tolerances for CNC machining depend on the level of precision required by the customer:
- ISO 2768–m (medium): Medium tolerances, these are the most common and are applied when there is no specific indication from the customer.
- ISO 2768-f (fine): Precise tolerances, must be explicitly requested by the customer to achieve greater accuracy.
What are the surface roughness levels available?
We have two options for surface roughness of CNC machining:
- Ra 3.2 – N8: This is the standard roughness value for parts.
- Ra 1.6 – N7: It is a better surface roughness, which must be explicitly requested by the customer.
What kind of certificates can I apply for CNC machining?
Certificates available for CNC machining include:
- Reports from laser control
- Report from CMM (contact) control: You must specify the number of points to be checked and which ones. It is preferable to indicate it in the table.
- Profilometer report
- Roughness meter report
- Hardness Testing
- Eye Control Report
- 2nd level CNC report
How do I request a quote for CNC machining?
To request a quote, you must submit an RFQ (Request for Quotation). Quote times are usually fast, but they can vary depending on the complexity of the project.
What is the duration of a CNC machining process?
Production times depend mainly on the quantities required. For higher volumes, the times can be shorter thanks to automated production, which ensures high efficiency.
What is the advantage of using CNC technology?
CNC technology offers many advantages:
- High Precision: CNC machining is extremely precise, allowing very tight tolerances.
- High repeatability: The results are consistently repeatable, ensuring consistency throughout production.
- Convenience for high volumes: Being structured with highly automated production lines. A demand for large batches allows a significant economic advantage
Can I request certificates and controls during production?
Yes, you can request various certificates and controls, including quality, hardness, roughness and optical control reports, among others, to ensure that the processes meet the required standards.