Give your products superior durability and impeccable aesthetics
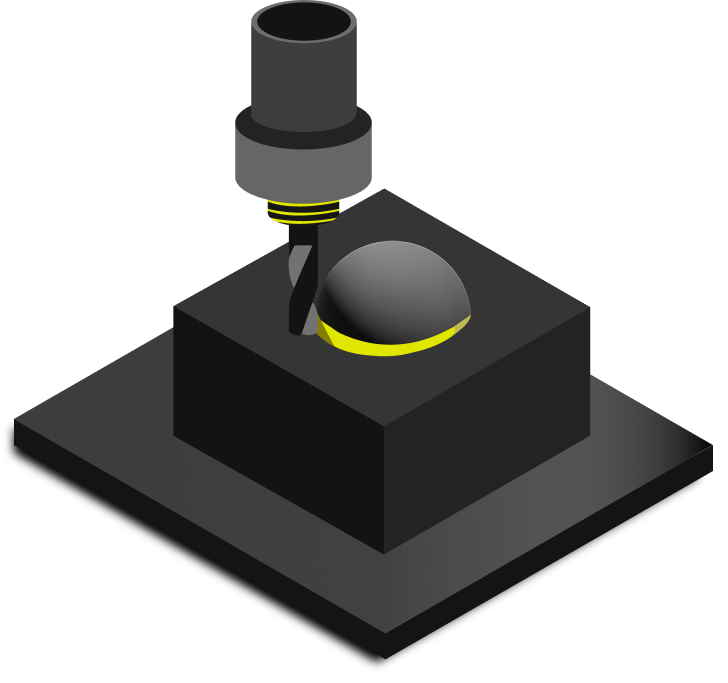
Post-processing of parts made with CNC machining
Anodization
Anodizing is an electrochemical process that increases the thickness of the natural oxide layer on the surface of metallic materials. During this process, the material is immersed in an electrolyte solution and an electric current passes through it. This treatment not onlyimproves resistance to corrosion and wear, but also allows for a more aesthetic and decorative surface.
FEATURES
- Improves corrosion resistance
- Increases surface hardness
- Allows aesthetic customization with different colors
- Available colors: red, blue, black, transparent
MATERIALS
- Aluminum and titanium
ADVANTAGES
- Benefits include longer material life, effective weather protection, and the ability to add different colors for aesthetic purposes.
polishing
Polishing is a surface finishing process that aims to improve the appearance and tactile quality of metal materials . During this process, the surface of the material is smoothed and polished using abrasives of various grain sizes, until a smooth and shiny finish is obtained. Benefits include the elimination of surface imperfections, an improved aesthetic appearance and reduced friction.
FEATURES
- Improves the aesthetic appearance and tactile quality of metallic materials
- Eliminates surface imperfections, making the surface smooth and shiny
- Reduces friction, improving material performance
- Increases corrosion resistance and facilitates maintenance
MATERIALS
- Aluminium and steel
ADVANTAGES
- Polishing gives it a professional look, while also improving corrosion resistance and making it easier to clean and maintain the material.
Electropolishing
Electropolishing is an electrochemical process used to improve the surface of metallic materials. The material is immersed in an electrolyte solution and an electric current is applied to remove a thin layer of metal from the surface. This process not only reduces roughness, but also increases gloss and corrosion resistance and reduces surface contamination.
FEATURES
- Reduces surface roughness
- Increases the shine of the material
- Improves corrosion resistance
- Facilitates cleaning and maintenance of the material
MATERIALS
- Stainless steel
ADVANTAGES
- Electropolishing improves the surface, increases corrosion resistance and facilitates cleaning, reducing surface contamination.
Burnishing
Burnishing is a surface finishing process that gives a dark, uniform appearance to metallic materials. During this treatment, the metal is immersed in a specific chemical solution that causes a surface reaction, creating a protective layer of oxides. This layer enhances the aesthetics of the material, giving it a sleek and professional finish, but also increases its corrosion resistance.
FEATURES
- Creates a protective layer of oxides
- Enhance aesthetics with a dark, uniform finish
- Increases corrosion resistance
- Reduces friction and improves material durability
MATERIALS
- Steel
ADVANTAGES
- Burnishing improves the durability of the material, reduces friction and optimizes weather resistance.
CHROMIUM PLATING
Chrome plating is a surface finishing process that involves applying a thin layer of chromium to metallic materials. During this treatment, the material is immersed in a chromium-containing solution and an electric current passes through it, which causes chromium to be deposited on the surface. This process gives it a shiny appearance, while also improving the corrosion and wear resistance of the material.
FEATURES
- Increased durability and wear resistance
- Smooth and shiny surface
- Increases corrosion resistance
- Optimized weather resistance
MATERIALS
- Steel and brass
ADVANTAGES
- Benefits include increased durability, a smoother, shinier surface, and effective protection against weather and chemicals.
Electroless nickel plating
Electroless nickel plating is a finishing process that involves the deposition of a layer of nickel on metal surfaces without the use of an electric current. This process takes place by chemical reaction, in which the metal is immersed in a solution containing nickel ions. This treatment is particularly appreciated for its ability to give durability and shine to the treated materials.
FEATURES
- Uniform coverage on complex surfaces
- Increased corrosion and wear resistance
- Improvement of the aesthetic properties of the material
- Conferring durability and shine to treated materials
MATERIALS
- Steel
ADVANTAGES
- Benefits include uniform coverage, corrosion and wear resistance, and improved aesthetic properties.
Peening
Shot peening is a finishing process that improves the surface of metal materials through the use of small abrasive balls. During this treatment, the balls are fired against the surface of the metal at high speed, creating a series of impacts that smooth and compact the material. Shot peening gives a uniform finish and can remove any surface imperfections.
FEATURES
- Increased fatigue and corrosion resistance
- Improved component life
- Uniform surface finish
- Removal of surface imperfections
MATERIALS
- Steel
ADVANTAGES
- Benefits include increased fatigue and corrosion resistance, improving component life
Cataphoresis painting
Cataphoresis painting is a process used to apply a uniform and resistant coating to metallic materials. Metal pieces are immersed in a water-based paint solution and subjected to an electric current that causes the paint to settle evenly on the surface. It provides complete coverage, even on complex surfaces, and improves the corrosion resistance and durability of the material.
FEATURES
- Effective protection against weather and chemicals
- Consistent finish on complex surfaces
- Increased corrosion resistance
- Reduced maintenance costs
MATERIALS
- Steel
ADVANTAGES
- Benefits include excellent protection against weather and chemicals
POWDER COATING
Powder coating is a surface finishing processin which a fine powder is applied electrostatically to metallic materials. During this treatment, the metal is electrically charged, allowing the powder to adhere evenly. Next, the workpiece is heated in an oven, melting the powder and creating an even, durable coating.
FEATURES
- Improves the aesthetic appearance of steel
- Uniform and durable coating through workpiece heating
- Increased corrosion resistance
- Homogeneous finish without dripping
MATERIALS
- Steel
ADVANTAGES
- Benefits include a homogeneous finish without dripping, improving the aesthetic appeal and durability of the treated materials.
ZINCIFICATION
Galvanizing is a finishing process that applies a protective layer of zinc to the surface of metallic materials to protect them from corrosion. It can be done by hot dipping, where the material is immersed in a bath of molten zinc, or by electrolytic processes, where the zinc coating is applied using an electric current. O offers an easy to maintain surface, increasing the useful life of the product.
FEATURES
- Protection against rust and weather
- Increased durability of the material
- Improved esthetic properties
- Surface easier to clean and maintain
MATERIALS
- Steel
ADVANTAGES
- Benefits include protection against rust and weathering, durability of the material, and improved aesthetic properties.
PASSIVATION
Passivation is a chemical process used to improve the corrosion resistance of metals. During this treatment, the material is immersed in an acidic solution that removes contaminants and surface oxides, creating a protective layer of chromium oxide.
FEATURES
- Improved corrosion resistance
- Increased durability of the material
- Prevention of rust and corrosion
- Extending the service life of the final product
MATERIALS
- Aluminum, stainless steel
ADVANTAGES
- Benefits include increased durability and weather resistance, preventing rust and other forms of corrosion, extending their service life.